The COVID-19 pandemic has heightened the need for sanitary environments across all industries. As the concern for hygiene has grown, both workers and customers are increasingly demanding cleaner, more hygienic spaces—especially in high-traffic areas. In response, industrial designers are opting for protective and sanitary solutions like hygienic wall cladding.
Hygienic wall panels, also known as antimicrobial surfaces, have gained popularity for their ability to combat bacteria, mold, and viruses, making them an excellent choice for spaces that require high sanitation standards. These panels not only help reduce the spread of germs but also resist stains and high-impact damages. They can be installed easily and quickly, ensuring your space remains clean and safe.
Let’s explore the science behind antimicrobial wall cladding and how it can improve your environment.
How Do Hygienic Panels Work?
Bacteria, mold, fungi, and viruses are often transmitted through contact with contaminated surfaces or via airborne particles. Hygienic wall cladding works by preventing the growth of these microorganisms, providing a protective barrier. Once installed, these antimicrobial surfaces begin to act immediately—if a sick person touches the wall, the antimicrobial agents begin working against bacteria and viruses right away, continuously reducing microbial growth over time.
These panels provide continuous protection against bacterial spread, keeping environments sterile for longer periods. However, hygienic panels don’t replace regular cleaning routines, but rather complement them. When combined with daily cleaning practices, they enhance the overall sanitation of the space.
A prime example of an environment that would benefit from hygienic wall cladding is schools. In busy school corridors, where students touch walls frequently, the antimicrobial properties of the panels prevent the spread of germs. If a sick student touches the wall after coughing or sneezing, the panel works to stop bacteria from contaminating the area.
Schools are an excellent example of an environment that would benefit from hygienic panels. You could place them along school corridors to reduce the spread of bacteria to students and employees. If a student coughs or sneezes into their palm, then places their hand on the antimicrobial surface, the wall would immediately prevent the bacteria from spreading. Without the hygienic wall cladding, one sick student could facilitate bacterial spread throughout the school.
However, hygienic panels don’t eliminate the need for other cleaning measures. You use them in combination with regular cleaning practices to create an enhanced sanitary environment.
Hygienic panels usually consist of fiberglass-reinforced plastic. FRP panels are popular in many industries because of their lightweight consistency and easy maintenance. They consist of a plastic matrix reinforced with Fiberglass polymers, which creates a resilient surface. You can combine hygienic FRP panels to make a thoroughly sanitized area.
Overall, hygienic wall claddings can help you create a safe environment in any industry.
Why Choose Antimicrobial Surfaces?
Benefits of Hygienic FRP Panels
Choosing antimicrobial materials for your environment offers multiple advantages. Here are some reasons why hygienic wall cladding, especially fiberglass-reinforced plastic (FRP) panels, are a great choice for your space:
- Easy installation: You can install hygienic FRP panels directly over existing walls, allowing for a simple installation. If you want to add antimicrobial panels to an existing area, you can measure it, then install a panel of the same size. If you’re starting a new project, you can add hygienic wall claddings after the initial construction. Either way, the installation is simple and hassle-free.
- Affordability: Hygienic wall claddings are also a cost-effective choice. Instead of paying costly replacement expenses, you can install the panels directly over existing surfaces. The antimicrobial materials can protect your surfaces for longer periods than typical tiles, saving you money in the long term.
- Sanitary protection: The many sanitary benefits of antimicrobial surfaces make them worthwhile for all types of industries. The reduction of bacteria, viruses and mold growth keeps your workplace safe. Employees and visitors can feel protected and satisfied. The panels’ lack of porous material allows them to protect against bacterial growth for longer periods. Overall, you can maintain cleanliness with low effort.
- Durability: Hygienic FRP panels can outlast typical wall panels. They are highly resistant to impacts and don’t crack easily. Their smooth surfaces prevent bacteria and other growth from building in seams. While they still require regular cleaning, you can wipe them easily and extend their life span even further.
Overall, hygienic wall panels are a cost-effective and durable choice for any environment.
Who Needs Antimicrobial Surfaces?
Hygienic wall claddings are an advantage in many industries. The panels can keep work environments cleaner, creating a more positive experience for employees and visitors.
These are examples of environments that would benefit from hygienic wall panels.
- Hospitals and medical facilities: Health care is a prominent example of an industry with high sanitation requirements. It’s crucial to provide patients with high-quality care and keep employees safe. Health care facilities can apply antimicrobial surfaces in many areas, from surgical suites to hospital rooms and corridors. The panels make it easier to maintain a sanitized environment for patients and staff alike.
- Food and beverage industry: The food industry also needs to meet high sanitation standards. Food preparation areas are susceptible to moisture and staining. Spills and moisture buildup can encourage bacterial growth, degrading the environment. Hygienic wall claddings can reinforce the area, improving stain resistance and creating a cleaner environment. You can install antimicrobial FRP panels in food preparation areas, food plants, sorting halls or storage rooms.
- Transportation: With over 30 million uses each weekday in America, public transportation has one of the highest traffic rates of any industry. From subway cars to bus stations, it’s crucial to maintain a safe environment for the many users around the country. Hygienic FRP panels can reduce the buildup of bacteria and microbes on walls and other high-touch areas. You can easily install them over existing walls in vehicles and transportation stations.
- Schools: Schools would also benefit from antimicrobial wall panels. They can reduce the spread of viruses and bacteria to the many students and employees in the building. With protection against bacteria growth and easier maintenance, the panels make it easier to maintain a clean environment for everyone.
Contact Stabilit America Today
Hygienic wall panels can help you create a safe environment. If you want to install a hygienic FRP panel, look no further than Stabilit America. Our inner wall and ceiling cladding can help you meet your high sanitation needs. And with our guaranteed simple installation, you can get started anytime. Whether you’re constructing new infrastructure or replacing a wall, our panels can be an ideal solution.
Our hygienic wall panels are perfect for many industries, including agriculture, health care, transportation and OEM. To get started with our hygienic inner walls, contact us today.
FAQs
What is hygienic cladding?
Hygienic cladding refers to wall coverings that have antimicrobial properties to prevent the growth of bacteria, mold, and viruses. These surfaces are often made of fiberglass-reinforced plastic (FRP) and are designed to be easy to clean and maintain.
What thickness should hygienic wall cladding be?
The thickness of hygienic wall cladding can vary depending on the application. Generally, a thickness between 1/8 inch to 1/4 inch is ideal for most environments, as it provides durability and impact resistance while maintaining ease of installation.
What is the best type of wall cladding?
The best type of wall cladding depends on the specific needs of the environment. For high-traffic and high-hygiene areas, fiberglass-reinforced plastic (FRP) cladding is one of the best choices due to its durability, antimicrobial properties, and ease of maintenance.
Stabilit America Inc. is a leading North American manufacturer of fiberglass reinforced panels (FRP) and polycarbonate sheets, with over 65 years of experience. The company offers the widest range of acrylic, polyester, and polycarbonate laminates, backed by international certifications (USDA, Greenguard, FM, ISO 9001, among others), serving industries such as industrial construction, transportation, and sustainable building.
Polycarbonate is acclaimed for its impressive strength and crystal-clear transparency, but its true resilience is often under-appreciated. In this exploration, we’ll uncover the robust properties of polycarbonate that contribute to its extensive lifespan, its formidable resistance to environmental stressors, and its standing against other market plastics. Stabilit America‘s advanced Macrolux polycarbonate resin panels serve as a prime example of this material’s enduring nature. If you’re searching for highly resistant, professional-grade solutions, these polycarbonate panels are setting new standards in long-term performance. For those wondering, is polycarbonate strong?—the answer is a resounding yes. Its performance under stress, impact, and extreme conditions puts it ahead of many alternatives.
Polycarbonate Longevity in Practice
Polycarbonate’s lifespan extends well beyond that of many plastics due to its innate resistance to wear and aging. Under normal conditions, such as those encountered in commercial and residential settings, polycarbonate panels can last for decades without significant degradation. Factors contributing to this longevity include the material’s resistance to yellowing and its ability to maintain optical clarity and physical properties over time.
Stabilit America‘s polycarbonate panels, backed by a solid warranty, reflect this endurance promise, providing users with a long-term solution for their structural needs. The resilience of these panels to everyday environmental stressors exemplifies the brand’s commitment to quality and sustainability, ensuring that customers receive not just a product but a lasting investment.
Resisting the Rigors of Nature: UV and Thermal Durability
Exploring further how durable polycarbonate is, particularly when facing harsh environmental elements, Stabilit America’s panels offer a prime example of enduring strength. UV exposure, often a critical factor leading to the deterioration of plastics, is mitigated by the UV-resistant coatings applied to these panels, preserving both function and form. This protective layer ensures that the panels do not become brittle or discolored, which are attributes that are pivotal for maintaining long-term performance.
Additionally, polycarbonate’s ability to withstand extreme temperature variations without compromising structural integrity is unmatched. It doesn’t warp or become fragile in cold weather, nor does it soften in heat, unlike many other plastics. These properties make Stabilit America’s polycarbonate panels highly suitable for diverse climates, from the sun-drenched tropics to the frosty poles, illustrating their global applicability.
Impact and Physical Durability of Polycarbonate
The impact resistance of polycarbonate is one of its most celebrated features, with a show of strength. Stabilit America’s polycarbonate panels are known for their ability to absorb violent impacts, resist shattering, and endure physical stresses that would easily damage other materials. This toughness makes them an ideal choice for high-risk areas prone to impact or abrasion.
In comparison to glass, polycarbonate exhibits up to 250 times more impact resistance, and unlike acrylic, it does not crack under stress. These properties are particularly beneficial in areas where safety is paramount, such as in protective barriers or sports facilities. The resilience of Stabilit’s polycarbonate also means less frequent replacements, ensuring that installations remain intact and perform optimally for years to come.
Enhancing Polycarbonate’s Strength
While polycarbonate is inherently strong, its durability can be further enhanced to suit specific industrial applications. Stabilit America employs a variety of treatments to boost the performance of their polycarbonate panels. Coatings to resist scratching and abrasion can extend the pristine appearance of the material, while advanced UV stabilizers protect against prolonged sun exposure.
For areas requiring additional safety measures, polycarbonate can be treated to be fire-retardant, self-extinguishing, and to stop the spread of flames. These enhancements ensure that Stabilit’s polycarbonate panels not only meet the demanding expectations of their customers but also provide a product tailored to the unique challenges of each application.
How Durable Is Polycarbonate vs. Other Plastics: A Comparative Study
So, how durable is polycarbonate? To answer the question, it’s crucial to compare it to other common plastics used in similar applications. Here’s a list highlighting how Stabilit America’s polycarbonate panels measure up against alternatives, providing insights into their unique benefits:
- Impact Resistance: Polycarbonate’s impact resistance is unparalleled, especially when compared to plastics like acrylic or PETG, which can shatter or crack upon impact. This makes polycarbonate the preferred material for safety installations and areas where potential impacts are a concern.
- Temperature Tolerance: Unlike PVC or ABS, which have limited thermal resistance, polycarbonate excels across a wide temperature range, maintaining performance from freezing conditions to extreme heat without deforming.
- UV Stability: Where other plastics may degrade and become brittle with prolonged UV exposure, Stabilit’s polycarbonate panels are treated with UV stabilizers, ensuring longevity even under constant sunlight.
- Fire Resistance: Safety is paramount, and in this regard, polycarbonate’s self-extinguishing properties are superior to many plastics. This characteristic is particularly crucial in applications where fire safety standards are stringent.
- Transparency and Light Transmission: For applications requiring clarity and light transmission, polycarbonate provides a clear advantage over opaque materials like PVC, offering a combination of transparency and strength that is hard to match.
- Flexibility and Fabrication: Polycarbonate is more malleable than many other plastics, allowing for more complex shapes and designs without the risk of cracking or breaking during the manufacturing process.
- Sustainability: At the end of its lifecycle, polycarbonate can be recycled, which cannot be said for all plastic materials. Stabilit America prioritizes sustainability, making polycarbonate an eco-conscious choice for customers.
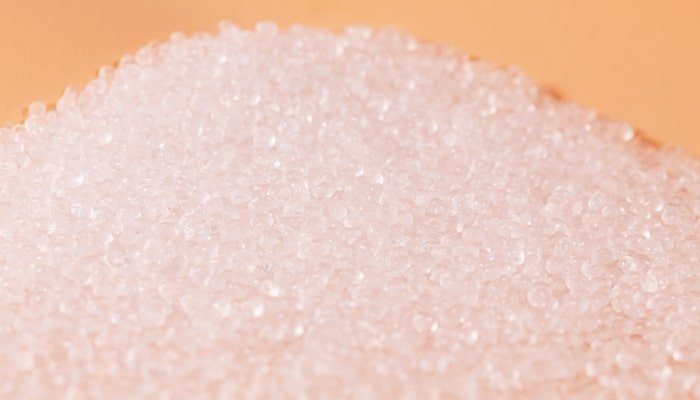
Secure Your Future with Stabilit Polycarbonate
The unmatched durability of Stabilit America’s polycarbonate panels is evident in their superior impact resistance, exceptional temperature tolerance, and outstanding UV stability. By choosing Stabilit’s polycarbonate solutions, you’re not just selecting a product—you’re investing in a legacy of innovation and environmental stewardship.
For those who demand the best in material performance and longevity, discover Stabilit America’s polycarbonate panels. Whether for industrial applications or creative architectural designs, these panels offer a clear advantage in durability and versatility.
Don’t settle for less. Contact FRP manufacturers like Stabilit America today to find out how our polycarbonate panels can elevate the durability and aesthetic of your next project. Choose Stabilit, and choose a future built on strength and clarity.
FAQs
Does polycarbonate break easily?
No, polycarbonate is highly impact-resistant and is up to 250 times stronger than glass. It doesn’t shatter upon impact, making it a safe and durable material for both indoor and outdoor applications.
What are the disadvantages of polycarbonate?
While polycarbonate is extremely durable, it can be more prone to scratching than glass. However, surface coatings can mitigate this issue. It may also cost more initially, but its long-term benefits often justify the investment.
Is polycarbonate stronger than steel?
While polycarbonate is not stronger than steel in terms of tensile strength, it is significantly stronger than many other plastics and is much more impact-resistant than glass or acrylic. Its combination of strength, light weight, and flexibility makes it ideal for numerous demanding applications.
Is polycarbonate strong?
Yes, polycarbonate is exceptionally strong. It offers high impact resistance, thermal stability, and durability, making it suitable for a wide range of demanding environments where traditional plastics or glass would fail.
Stabilit America Inc. is a leading North American manufacturer of fiberglass reinforced panels (FRP) and polycarbonate sheets, with over 65 years of experience. The company offers the widest range of acrylic, polyester, and polycarbonate laminates, backed by international certifications (USDA, Greenguard, FM, ISO 9001, among others), serving industries such as industrial construction, transportation, and sustainable building.
Step into the world of modern bathroom design, where Stabilit America’s FRP bathroom wall panels revolutionize the concept of style and functionality. Gone are the days of battling with grout lines and worrying over water damage. Our residential FRP panels offer a seamless, hygienic, and low-maintenance solution that stands up to the bustling demands of commercial bathroom spaces. With an array of benefits, including unparalleled durability, water resistance, and effortless cleaning, these panels are not just an addition to your bathroom—they are a smart investment in creating a spotless and welcoming environment. Whether you need wall protection or are considering high-performance FRP shower wall panels, this versatile solution brings peace of mind to any design.
Advantages of FRP Panels in Design and Construction
Transforming your commercial bathrooms begins with a choice that melds visual appeal with enduring quality. Stabilit America’s FRP bathroom wall panels are at the forefront, providing not just a surface but a canvas for creative expression. With a variety of textures and colors, these panels afford designers the flexibility to bring their vision to life while promising a lifespan that outstrips traditional materials. The non-porous nature of FRP resists moisture and mitigates mold growth, ensuring that the aesthetics are preserved from the relentless wear of humid environments.
Aesthetic Versatility and Longevity
FRP panels’ aesthetic versatility opens a realm of design possibilities, from sleek, contemporary motifs to rich, textured finishes that mimic natural materials. Their color retention is exemplary, standing steadfast against the fading effects of harsh cleaning agents and UV exposure. In the long game of wear and tear, FRP panels stand tall; they are resistant to scratches and impacts that would mar other surfaces. FRP panels from Stabilit America not only elevate the aesthetic of your space but do so with a promise of longevity, reducing the need for frequent refurbishments.
Impact on Construction Timelines and Cost Efficiency
Unlike the labor-intensive process of laying tiles, FRP bathroom wall panels can be installed quickly and without the need for specialized skills. This expedited process can slash construction timelines, allowing for spaces to be operational sooner. The durability of FRP means fewer replacements and repairs—translating to cost savings over the lifespan of your bathroom space. In addition, the minimal maintenance required keeps ongoing costs low, offering an economic advantage from start to finish.
By embracing the advantages of FRP, you set the stage for a bathroom that not only impresses at first glance but also delivers unwavering performance year after year. Let these panels be the cornerstone of a space that stands the test of time both in style and structure.
FRP vs. Traditional Bathroom Surfaces
When considering the materials for your bathroom surfaces, the choice between Stabilit America’s FRP bathroom wall panels and traditional tile is not to be taken lightly. It’s a decision that affects not just the present aesthetics but also the future of maintenance and hygiene within your facilities. Let’s break down the differences to guide your decision:
Installation Time: FRP panels are notably quicker to install than traditional tile. Tiles require individual placement and grouting, a process that FRP panels streamline significantly. The quick and easy installation of FRP panels means less downtime for your facilities and swifter project completion.
Water Resistance: While tiles are resistant to water, grout is not without its vulnerabilities. FRP panels offer a seamless surface that stands up to moisture without the weak points of grout lines. In environments with high humidity or direct water exposure, FRP panels maintain their integrity far better, reducing the risk of mold and water damage.
Durability: Tiles can crack and chip, necessitating replacements and repairs. FRP panels, however, are impact-resistant and less likely to suffer damage from everyday wear and tear. The long-term durability of FRP panels often translates to reduced repair and replacement costs.
Aesthetic Longevity: The grout used with tile can discolor and stain, while FRP panels maintain their appearance over time without the need for re-grouting or intensive cleaning. FRP panels sustain their new look with simple cleaning routines, avoiding the labor-intensive process of keeping grout pristine.
In the long run, the benefits of choosing FRP bathroom wall panels from Stabilit America become ever more apparent. The low maintenance nature of FRP translates to ongoing cost savings and reduced labor. Hygienically, FRP panels offer a non-porous surface that resists the growth of mold and bacteria, which is a critical factor in environments where cleanliness is extremely important.
Tailored for Bathrooms: Selecting the Right Panels
In your quest for the ideal bathroom, the materials you choose play a pivotal role in the long-term functionality and health of the space. Stabilit America’s FRP panels are designed with these bathroom-specific challenges in mind, offering moisture resistance and antimicrobial properties that are essential in such a setting.
The Importance of Moisture Resistance and Antimicrobial Properties
Bathrooms, by their nature, are prone to damp conditions, which can lead to the growth of mold and bacteria. The moisture resistance of FRP bathroom wall panels is not just a feature—it’s a shield against these unwanted intruders, ensuring that walls remain dry and inhospitable to microbial growth. Moreover, the antimicrobial properties of these panels mean that surfaces are not just resistant to water but actively hostile to germs, providing a healthier environment for all users.
Guidelines for Choosing Panels Based on Specific Bathroom Needs
- Assess the Level of Exposure: Consider the amount of direct water contact the panels will face. Shower areas require the highest level of moisture resistance.
- Evaluate Usage Frequency: High-traffic bathrooms benefit from the durable nature of FRP panels, which can handle the wear and tear of constant use.
- Understand Cleaning Routines: Choose panels that can withstand the cleaning agents and methods your maintenance schedule employs.
- Consider Aesthetics and Functionality: Ensure that the panels fit the visual design of the bathroom while meeting practical requirements.
Selecting the right panels for your bathroom isn’t a decision to take lightly. Embrace the assurance that comes with panels that are as functional as they are aesthetically pleasing, and transform your bathroom into a sanctuary of cleanliness and style.
Forge a Future of Uncompromised Quality and Safety
Reach out to Stabilit America today and let us assist you in selecting the perfect FRP panels that cater to your specific needs. Together, we’ll craft spaces that aren’t just built to last but are designed to impress, protect, and serve impeccably, day after day.Contact us to get started.
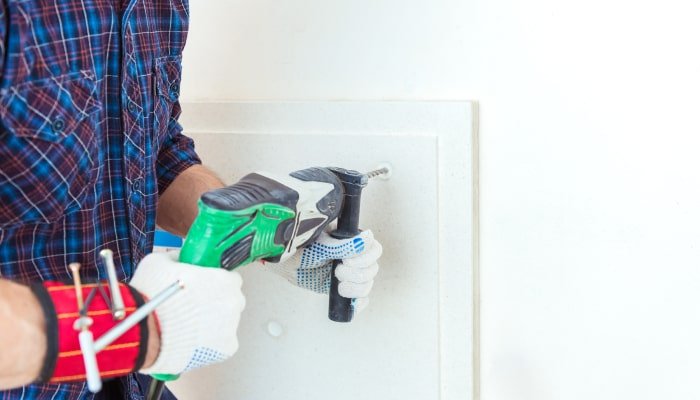
FAQs
Are FRP panels good for shower walls?
Yes, FRP panels are excellent for shower walls due to their seamless, non-porous surface that resists water and inhibits mold and mildew growth. Their durability also makes them ideal for high-moisture environments like showers.
What are the disadvantages of FRP panels?
While FRP panels offer many benefits, they can be less heat-resistant than other materials and may require proper wall prep before installation. However, their long-term performance and ease of maintenance often outweigh these concerns.
Is FRP wall panel waterproof?
Yes, FRP wall panels are inherently waterproof. Their non-absorbent surface ensures reliable moisture resistance, making them suitable for bathrooms, showers, and other high-humidity areas.
Stabilit America Inc. is a leading North American manufacturer of fiberglass reinforced panels (FRP) and polycarbonate sheets, with over 65 years of experience. The company offers the widest range of acrylic, polyester, and polycarbonate laminates, backed by international certifications (USDA, Greenguard, FM, ISO 9001, among others), serving industries such as industrial construction, transportation, and sustainable building.
If you are an industry expert, you have probably worked with a wide range of materials in numerous construction projects. Among the many available options, polycarbonate roofing sheets stand out due to their combination of strength, light weight, and flexibility. Their use as a roofing material has grown exponentially due to these benefits. However, like any building material, the key to maximizing polycarbonate’s advantages lies in correct installation. This article provides a detailed, step-by-step guide to installing polycarbonate roofing sheets effectively and professionally.
Understanding Polycarbonate Roofing
The best way to know how to install polycarbonate roofing sheets is to understand the material you are working with. Polycarbonate is a robust thermoplastic material known for its high impact resistance, light transmission, and adaptability. Roofing sheets made from polycarbonate are available in various types, including corrugated sheets and multi-wall (twin-wall, triple-wall, or multi-wall) sheets. The installation process varies slightly depending on the type of sheet and the specific project requirements.
Essential Tools and Materials
Before you start, ensure you have the necessary tools and materials. These typically include:
- Polycarbonate roofing sheets
- Polycarbonate-compatible screws and washers
- Measuring tape
- Circular saw or tin snips
- Drill
- Silicone sealant
- Anti-dust tape
- Polycarbonate flashing and capping
- Safety goggles and gloves
Step-by-Step Installation Process
- Safety First: Always start by ensuring your safety. Wear safety goggles, gloves, and sturdy footwear throughout the installation process. If working at a height, use secure ladders or scaffolding.
- Planning and Measuring: Begin by planning your layout and measuring the area to be covered. This helps determine the number of sheets, purlins, or rafters needed. Remember to allow for an overhang on the gutter of at least 50mm.
- Cutting the Sheets: If necessary, cut the sheets to size using a fine-toothed circular saw for straight cuts. Peel back the protective film on the cut areas to prevent melting and sticking. Always cut the sheets on a flat surface.
- Pre-drilling Holes: Since these sheets expand and contract with temperature changes, pre-drill oversized holes for the screws. Holes should be 10% larger than the screw shank diameter.
- Sealing the Edges: Seal the top end with solid polycarbonate tape and the bottom end with anti-dust tape. This keeps dirt, insects, and moisture out and stops water from wicking upward through capillary action.
- Positioning the Sheets: Start from the opposite end of the prevailing wind. Place the first sheet onto the purlins with the UV protective layer facing upwards. Ensure proper overhang at both the roof and gutter ends.
- Fixing the Sheets: Secure the sheet using compatible screws and washers. Avoid overtightening. Washers should be compressed but still visible. Overlap the sheets by at least one corrugation or as recommended.
- Sealing the Joints: Apply a bead of silicone sealant to the side lap where each sheet overlaps to prevent water ingress.
- Installing Flashing: Install ridge flashing or capping over the roof peak joints. Seal both sides with silicone sealant. This step improves waterproofing and enhances aesthetics.
- Finishing Touches: Inspect all connections, verify that screws are secure but not over-tightened, and make sure joints are sealed completely.
Tips for Successful Installation
- Weather Considerations: Install on mild days to minimize expansion or contraction.
- Handling the Material: Keep the protective film on until fully installed to prevent scratches.
- Cutting Sheets: Use high-speed, fine-toothed blades and avoid forcing the blade.
- Screw Placement: Place screws at the crest for roofing and valleys for wall panels.
Explore Stabilit America’s product catalog for polycarbonate solutions tailored to roofing and facade systems.
Maintenance Post-Installation
Proper installation is critical, but so is regular maintenance. Clean the surface with warm soapy water and a soft cloth. Avoid abrasive tools or harsh chemicals. Inspect periodically for damage or loose components. Replace any compromised sheet immediately to preserve roof performance.
Wrapping Up the Installation Guide
Now you know the essentials of how to install polycarbonate roofing sheets! They are an excellent choice for numerous applications due to their durability, light transmission, and versatility. However, their benefits can only be fully realized with correct installation and maintenance. While the process may seem complex, understanding each step and taking a step-by-step approach can make the task manageable.
Whether you are a construction professional or a DIY enthusiast, we hope this comprehensive guide provides valuable insights into the installation of polycarbonate roofing sheets. Remember, safety should always be your priority, and when in doubt, don’t hesitate to seek professional advice. Happy building!
Whatever roofing solution you need, Stabilit has got you covered!
Macrolux Solid compact sheets are the perfect roofing solution when you need great impact resistance and excellent light transmission. Some applications include: glazing, parapets, canopies, skylights, curved roofing systems, signage in general, neon signs, road signs, and noise barriers. Macrolux Solid sheets come in thicknesses ranging from 3 mm to 15 mm, in a choice of translucent and opaque colors.
Stabilit has a material that fits your needs. Contact us and find out more about how we can help!
FAQs
What are the benefits of polycarbonate roofing sheets?
They offer superior impact resistance, UV protection, and light transmission while being lightweight and durable.
Can polycarbonate roofing be installed by a non-professional?
Yes, with the right tools and precautions, DIY installation is possible. However, professional support is recommended for large or complex roofs.
Do polycarbonate roofing sheets need maintenance?
Yes. Routine cleaning and visual inspections help maintain clarity and structural integrity over time.
How long do polycarbonate roofing sheets last?
When installed and maintained correctly, polycarbonate sheets can last 10 to 20 years or longer.
Where can I purchase polycarbonate roofing sheets?
You can contact Stabilit America to find the right solution and get expert support.
Stabilit America Inc. is a leading North American manufacturer of fiberglass reinforced panels (FRP) and polycarbonate sheets, with over 65 years of experience. The company offers the widest range of acrylic, polyester, and polycarbonate laminates, backed by international certifications (USDA, Greenguard, FM, ISO 9001, among others), serving industries such as industrial construction, transportation, and sustainable building.
Temperature changes, different types of climates, pollution, and sunshine are some of the factors that have an effect on man-made structures. This leads to phenomena such as cracks, abrasion, sinking, breakdown, and deformation. Additionally, other effects can show up in structures, such as efflorescence and delamination. Often, and concerningly so, degradation or breakdown symptoms can appear. When this happens, materials are not recoverable. This makes you wonder: exactly what does “corrosion resistant” mean?
What is corrosion resistance?
Most structures are planned and erected with long-term use in mind. Because of this, the conditions they will face need to be considered and planned for, especially if they are commonplace, such as weather, pollution, and sunlight. This consideration and planning leads to actions intended to prevent wear, prolong useful life, and limit service interruptions due to maintenance. A fundamental step in this direction is choosing the right materials from the beginning. Given that wear and degradation due to chemical or electrochemical reactions is common, it is important to be very clear on what exactly corrosion resistance means, so that we can select a product that truly performs as we need it to.
To understand how certain materials are able to prevent corrosion and the importance of preventing it, we must be clear on what it is. Corrosion is the deterioration of materials as a result of chemical and electrochemical reactions. Corrosion as deterioration or wear usually refers to metals, because when it comes to ceramics and polymers, it is called degradation.
Corrosion is a natural phenomenon that is influenced by the material that undergoes deterioration, the environment, and, frequently, water. It is also possible to find other substances that can cause corrosion. These are called corrosive substances, and some of them include:
- Perchloric acid
- Nitric acid
- Sulphuric acid
- Chlorhydric acid
- Formic acid
The speed at which corrosion sets in depends on the factors involved. Regardless of the reasons that apply in each case, material deterioration due to electrochemical reactions is a concern for those involved in the construction industry, as it causes damage and financial losses.
Types of corrosion
There are several ways to classify corrosion, but there is one approach that is the most comprehensive, because it contains all possible kinds of corrosion. Dividing corrosion into chemical and electrochemical allows us to classify deterioration according to types of materials and the reaction taking place.
- Chemical: This form of corrosion takes place when a material reacts to a corrosive substance until it is either dissolved or it saturates the material. This classification includes chemical attack, selective lixiviation, and chemical metal attack.
- Electrochemical: Occurs when there is a loss of electrons from atoms, turning them into ions. This category contains galvanic, microbiological and superficial aeration corrosion.
Is corrosion the same as oxidation?
Oxidation and corrosion are not the same; although oxidation does cause a change in materials, it is just a superficial reaction. It occurs when oxygen comes in contact with other substances, such as metals. In the case of metals, brown discolored spots can be observed. This is oxide.
Because oxidation happens only on the surface, it can be removed, as opposed to corrosion, which implies a structural deterioration. In some cases, oxidation is considered a precursor to corrosion. Steps should be taken to control the former, in order to prevent the latter. Damage from corrosion is irreparable.
Corrosion resistance
The term refers to the capacity some materials have to resist the damage that can result from coming in contact with other substances or the environment.
Corrosion resistance can be a property of a material, or can be attained by adding another substance to the product. This additional substance may bring forth the desired resistance. Such is the case with metals that frequently rely on coatings, alloys or paints that can delay or completely prevent corrosion.
Are Stabilit products corrosion resistant?
One of the simplest solutions to avoid corrosion and prevent maintenance costs in any structure is to use materials designed with anticorrosive qualities. Of course, Stabilit manufactures laminated plastics considered corrosion-resistant. They are designed to provide engineers, architects, builders, contractors, and property owners a modern solution, reinforced with fiberglass, to meet their needs. FRP panels like those manufactured by Stabilit offer superior corrosion resistance, performance, and versatility.
Resolite
The Resolite brand includes products composed with polyester, which boosts corrosion resistance. This was our first product line to include a fire retardant option (Resolite CR) in its lineup of plastic laminates.
Resolite provides multiple options so that any building or structure can succeed at meeting its requirements. Resolite CR-RFM is a strong opaque laminate that meets the Factory Mutual standards for fire resistance and wind resilience.
Resolite (RFM) is produced using a high-quality polyester resin system with a protective barrier that binds with the resin and fiberglass matrix. The result is a panel much more protected against degradation and with great durability.
Opalit
Another anticorrosive polyester sheet that is part of the Stabilit America product line is Opalit. In the last decade several new materials have been developed that can fulfill performance requirements similar to metallic laminates, but with none of their downsides. Opalit is such a product.
Opalit for Cooling towers can handle the extremely corrosive environments of cooling towers. It is designed specifically for use in louvers, stair enclosures and exterior casings. Opalit for Agricultural applications is engineered to withstand the ammonia gasses from chickens and pig waste. This makes it ideally suited for roofing and ceilings in poultry and hog farms. It is strong and durable, while also aesthetically pleasing. Its Gelcoat finish protects against UV rays, humidity and pollution, while preventing the dreaded fiber bloom and aging that plagues other brands. There is a fire-retardant option available as well.
Key Benefits of Stabilit FRP
Because they are so strong, FRP sheets can last over 20 years and are highly resistant to corrosion and humidity. Here are some key benefits when compared to metal sheets:
- Cost savings
- Strength and mechanical resistance
- Low thermal conductivity
- Design flexibility
- Longer useful life
- Better surface finish
- Electrical insulation properties
- Vibration reduction and noise dampening
- Lighter by 40 to 50%
- Flexibility
- Corrosion resistance
- Minimal maintenance
- Impact resistance
- Resists the elements, acids, and humidity
If you want to know more about corrosion-resistant materials for the industrial and agro-industrial sectors, you need to dive into fiberglass-reinforced plastics. Visit our page “What is FRP?” to learn more about this. When building any structure, it is better to anticipate maintenance costs and choose the best, high-quality construction materials.
Stabilit America: technology, strength, quality, and aesthetics for every one of your projects
At Stabilit America we produce and distribute materials that truly support your success. For construction, remodeling or even transportation projects, our quality and technological innovations deliver results. Whether you want strength, durability, a better cost-benefit ratio, light transmission, compatibility, thermal insulation or UV protection, we have the key material to get you where you are trying to go.
We manufacture fiberglass-reinforced polymer panels and polycarbonate sheets that can integrate effectively into any modern construction project. They provide benefits such as UV protection or microbe resistance, depending on the needs of your project. Which of our solutions is the best fit for your needs?
Acrylit
Glasliner
Macrolux Multiwall
Macrolux Rooflite
Macrolux Solid
Macrolux AM
Opalit
Resolite CR
Polylit
Acryloy CR
Versalit
Interior and exterior walls, roofs, covers, skylights, canopies, luggage and cargo boxes, truck walls… for any industrial, institutional, commercial or transportation project, Stabilit has a material that fits your needs. Contact us and find out more about how we can help!
FAQs
What does corrosion-resistant mean in construction?
It refers to a material’s ability to withstand environmental or chemical exposure without degrading over time, ensuring longevity and reduced maintenance.
What types of materials are corrosion-resistant?
FRP panels, stainless steel, aluminum with protective coatings, and polymer composites are among the most effective corrosion-resistant materials.
Why should I choose FRP panels over metal sheets?
FRP panels offer better corrosion resistance, require less maintenance, and are lighter and easier to install. They are also more adaptable to harsh environments.
Where can I buy corrosion-resistant FRP panels?
You can explore and purchase FRP panel solutions directly through Stabilit America or contact our team to receive tailored guidance.
Stabilit America Inc. is a leading North American manufacturer of fiberglass reinforced panels (FRP) and polycarbonate sheets, with over 65 years of experience. The company offers the widest range of acrylic, polyester, and polycarbonate laminates, backed by international certifications (USDA, Greenguard, FM, ISO 9001, among others), serving industries such as industrial construction, transportation, and sustainable building.
Installing fiberglass reinforced polymer (FRP) panels on RV exterior walls provides a durable, weather-resistant surface that improves the functionality and look of your recreational vehicle fleet. Getting the installation right keeps your vehicles on the road longer and keeps your customers happy. Here’s a detailed guide from Stabilit America on how to properly install your Versalit exterior fiberglass wall and roof panels. These high-performance FRP panels are engineered for strength and longevity in even the most demanding environments.
Preparing for Installation
The first step when you are ready to start installing your Stabilit FRP panels on your RV sets you up for a smooth process. Don’t just jump right in—make sure everything is ready. Your tools should be on hand, and you might want to create a checklist. Additionally, you’ll want to make sure that your workspace is clean and dry to prevent any problems when you start the adhesion process. Paying close attention here helps you get long-lasting results.
Gathering Materials: Gather all of the necessary tools and materials before you start and put them in the right place. Don’t forget that this includes safety gear like gloves and goggles to protect against dust and debris.
Workspace Preparation: Clean your workspace thoroughly. Remove any debris, dust, or moisture that might compromise the adhesive’s effectiveness or the panel’s integrity.
Tool Check: Make sure each of your tools is in good working order. A blunt saw or an unevenly notched trowel can cause some serious issues during the cutting and application phases, and it may even damage the panels, which would result in wasted materials.
A well-prepared start leads to a successful installation of your Versalit exterior fiberglass wall panels, setting the tone for the task ahead.
Measuring and Cutting the Panels
Accurate measurement and precise cutting are extremely important for the successful installation of the FRP panels on your RV. Start by carefully measuring the installation area to figure out the exact size of the panels required. Make sure you allow for a quarter-inch gap around the perimeter of each panel to accommodate any expansion from temperature changes.
Taking Measurements: Measure the height and width of the installation area. Use a tape measure for accuracy and note down these measurements.
Panel Marking: Transfer these measurements onto your FRP panels, clearly marking where you need to make the cuts. Make sure all of your markings are visible and straight for accurate cutting.
Cutting the Panels: Use a table saw or circular saw to cut the panels along your markings. Keep the panel face up to avoid surface damage and ensure a clean, sharp edge.
Once you’re done, check each cut panel to make sure it fits the area on your RV before starting to do anything with the adhesive application. Taking the time to do this extra step will prevent the hassle of adjustments mid-installation.
Applying Adhesive
Proper adhesive application is what allows your FRP panels to withstand the rigors of the road. Choose an adhesive that offers moisture resistance to handle the external conditions of an RV. The goal is to create a reliable bond that stands up to both movement and weather.
Choosing Adhesive: Select a high-quality, moisture-resistant adhesive that is compatible with FRP panels to get optimal performance outdoors.
Application Technique: Spread the adhesive evenly across the panel’s backside using a notched trowel. The notches help create a uniform pattern that improves the grip between the wall and the panel.
Coverage Check: Make sure you get complete coverage and don’t leave any gaps to prevent any weak points that might lead to panel separation or water ingress later on.
After applying the adhesive, give it some time to become tacky, as this improves the bond strength when the panels are applied.
Installing the Panels
How you install FRP panels requires precision and attention to detail so that your exterior wall panels are aligned and securely attached. Position the panel on the prepped surface, applying firm, even pressure to create a strong bond.
Positioning: Align the panel carefully with your marked measurements. Make sure it fits perfectly within the designated space.
Securing the Panel: Firmly press the panel against the wall using a laminate roller to smooth it down and eliminate any air bubbles.
Observing Expansion Gaps: Stay vigilant about maintaining the necessary expansion gaps. These gaps are extremely important because they allow the panels to expand and contract with temperature changes without warping or buckling.
Once all of your exterior wall panels are installed, do a walk around and inspect each one to check for loose edges or visible gaps.
Sealing and Finishing
Finalizing the installation with proper sealing and finishing touches protects the integrity of your FRP panels and extends their lifespan. This step helps safeguard against moisture and keeps the panels functional in all weather conditions.
Applying Sealant: Use a high-quality silicone sealant around all of the edges and within expansion gaps to create a waterproof barrier.
Additional Waterproofing: In areas particularly susceptible to water exposure, apply an extra layer of waterproofing sealant to fortify the panels against moisture ingress.
Visual Inspection: After sealing, check the entire installation for any missed spots or potential vulnerabilities that could lead to issues in the future.
Effective sealing prevents moisture damage and reinforces the overall structure.
Maintaining and Cleaning
Regular maintenance is going to be necessary to keep the newly installed FRP panels in pristine condition. This helps preserve their appearance and keeps them performing their protective role effectively.
Routine Cleaning: Use mild detergents and a soft cloth or sponge to clean the panels. Regular cleaning prevents dirt build-up.
Addressing Tough Stains: For more stubborn stains, use specialized FRP cleaners that tackle grease and other residues without damaging the surface.
Inspect Regularly: Periodically inspect the panels for any signs of wear or damage. Addressing these issues can prevent larger problems down the line.
Proper maintenance of your Versalit exterior fiberglass wall panels helps extend their life and keeps them functioning under harsh road conditions. Regular care is straightforward and helps avoid costly repairs for your fleet.
Ready to Upgrade Your RV? Choose Versalit Panels Today!
Ready to enhance the durability and look of your RV fleet? Versalit exterior fiberglass panels and fiberglass roof panels offer the strength, style, and sustainability you need. Make sure your RV is equipped to handle any adventure. Contact us about FRP Panels to find out more about our innovative solutions and start your journey toward a stronger, more stylish RV.
FAQs
What do you put behind FRP panels?
Behind FRP panels, a clean, dry, and structurally sound surface like plywood or drywall is typically used. It should be free of any contaminants to ensure proper adhesion and long-term performance.
How do you secure FRP panels?
FRP panels are secured using high-quality construction adhesive along with mechanical fasteners if needed. A notched trowel helps apply the adhesive evenly, while a laminate roller ensures strong bonding to the wall surface.
Is FRP easy to install?
Yes, FRP panels are relatively easy to install with basic tools. Their lightweight design, combined with simple cutting and adhesive application methods, makes them suitable for both professionals and DIY enthusiasts.
Stabilit America Inc. is a leading North American manufacturer of fiberglass reinforced panels (FRP) and polycarbonate sheets, with over 65 years of experience. The company offers the widest range of acrylic, polyester, and polycarbonate laminates, backed by international certifications (USDA, Greenguard, FM, ISO 9001, among others), serving industries such as industrial construction, transportation, and sustainable building.
Corrugated fiberglass roofing sheets are versatile and durable materials that you can use effectively for your residential, industrial, and agricultural projects. These unique panels are well known for their lightweight structure and high-impact resistance, offering excellent performance even under extremely challenging conditions. At Stabilit America, we manufacture our fiberglass roof panels using high-quality fiberglass and advanced resins, so they provide the best protection against environmental factors. They are a reliable choice for long-term roofing solutions, particularly when compared to metal or other less weather-resistant alternatives.
The Advantages of Stabilit America’s Corrugated Fiberglass Sheets
Corrugated fiberglass roof sheets offer a number of benefits that set them apart in the roofing market and answer the question: are fiberglass roof panels worth it? From extended durability to visual appeal, their value lies in a perfect balance of form and function.
Corrosion Resistance
Stabilit America’s corrugated fiberglass roofing sheets have a resistance to corrosion. Metal roofing materials can deteriorate when they get exposed to moisture, chemicals, or salt-laden air. On the other hand, fiberglass panels maintain their structural integrity over time. They work great in environments where your materials could get exposed to humidity, industrial chemicals, or coastal conditions that pose a challenge to longevity. With corrosion-resistant properties, these sheets need less maintenance, and they’ll continue to perform reliably even in harsh settings. When you choose fiberglass over metal, you extend the lifespan of your roofing system while avoiding costly repairs associated with rust and material degradation.
High Light Transmission
Our sheets offer a light transmission rate of up to 90%. They are ideal for any space where natural light is a priority. For greenhouses and skylights, this feature allows you to create the most optimal environment that allows for plant growth while reducing reliance on artificial lighting. The frosted glass appearance in certain models can also improve light diffusion, creating a bright, even illumination across your space. This design is special because it improves visibility while also contributing to energy efficiency by lowering electricity costs associated with lighting.
Exceptional Weather Resistance
Durability in extreme weather is one of the best features of Stabilit America’s fiberglass sheets. With UV protection and the ability to withstand hail impacts of up to 19 mm in diameter, they maintain their structural integrity even in extremely severe conditions. The resistance to surface erosion that you get with corrugated fiberglass roofing sheets provides you with long-lasting performance and provides your customers with dependable shelter year-round. Whether you’re building in an area with intense heat, heavy rain, or freezing temperatures, you’ll get reliable protection without compromising appearance or functionality.
Fire Resistance
Certified as self-extinguishing, our corrugated fiberglass sheets play an extremely important role in improving building safety. Unfortunately, some of the more traditional materials could actually spread flames, but Stabilit America’s fiberglass sheets work to stop the propagation of fire. This feature is particularly valuable in commercial and industrial settings where safety regulations require fire-resistant materials. Their fire-resistant properties offer peace of mind while meeting stringent safety standards, adding an extra layer of protection to your roofing system.
Ease of Installation
Lightweight and easy to handle, you’ll be impressed by the installation process. You can effectively reduce the labor time required and the associated costs that come with a more complex installation. You can cut them with standard tools, so you can also use them for a wide range of project requirements. The overlapping design ensures a secure fit and improves their water resistance, preventing leaks and reducing maintenance needs. For builders and contractors, these features translate to efficient workflows and high-quality results in less time.
Applications for Corrugated Fiberglass Roofing Sheets
Corrugated fiberglass roofing sheets stand out for their adaptability across various industries and projects. Their lightweight, durable design makes them a practical choice for any project that requires reliable performance under varying conditions. Whether you’re looking to invest in the right roofing materials for agricultural, residential, or commercial purposes, these sheets offer specific benefits tailored to each application.
Industrial Buildings
Industrial facilities need roofing materials that can withstand exposure to moisture, chemicals, and extreme temperatures. Corrugated fiberglass sheets work great in these conditions because of their corrosion-resistant properties. They have become a superior alternative to traditional metal roofing that will improve the durability of your structure. They do not rust or weaken over time, even in environments where with high humidity or chemical fumes. Their lightweight structure also allows for easier installation without compromising durability, reducing overall construction time. Additionally, the sheets’ ability to withstand heavy impacts and extreme weather conditions makes them a long-term solution for industrial applications where reliability is important.
Greenhouses and Skylights
Corrugated fiberglass sheets are a popular choice for greenhouses and skylights due to their exceptional light transmission and UV protection. They allow up to 90% of natural light to pass through, creating an optimal environment for plant growth. This natural light then gets evenly diffused across the space as a way to promote healthier crops and reduce the need for artificial lighting. Additionally, their UV-blocking capabilities shield any plants in the greenhouse, and the people tending to them, from harmful rays. This helps prevent damage and allows for long-term productivity. The sheets’ resistance to hail and extreme temperatures creates even more stability and safety, even in harsh climates.
Residential Covers
These roofing sheets are commonly used in residential settings for their modern look and practical benefits. They work well for patios, walkways, and carports, providing reliable shelter while allowing natural light to illuminate the space. Homeowners appreciate their durability since they won’t yellow or crack over time. This is true even under prolonged sun exposure. Lightweight construction makes installation straightforward, reducing labor time and costs. With the added benefit of reducing glare and providing a sleek appearance, these sheets are a popular choice for enhancing outdoor spaces.
Commercial Spaces
In commercial settings, corrugated fiberglass sheets deliver both durability and aesthetic appeal. They can be used for canopies, sunrooms, and restaurant patios where functionality and design are both important. These sheets can withstand high wind loads and heavy rain, making them a reliable choice for areas exposed to unpredictable weather. Their translucent nature enhances the ambiance by providing natural light, while the self-extinguishing properties ensure added safety in public spaces. Easy maintenance and a long lifespan make them a cost-effective solution for business owners aiming to balance practicality with style.
Each application provides you with unique advantages, given their ability to perform reliably across various projects. When you use Stabilit America’s corrugated fiberglass sheets for your roofing project, you get a material that meets the demands of various environments without compromising on the quality and appearance you need.
Maintaining Corrugated Fiberglass Roofing Sheets
Proper maintenance is important to ensure you set the foundation for the longevity and optimal performance of your corrugated fiberglass sheets. Regular inspections and cleaning can prevent potential issues:
- Inspections: Check for any damage caused by debris or extreme weather. Promptly addressing minor cracks or dents can prevent larger issues.
- Cleaning: Use mild soap and water to clean the sheets, avoiding abrasive materials that may scratch the surface. Maintaining cleanliness prevents the accumulation of dirt and debris, which can affect light transmission.
- Ventilation: Ensure proper ventilation around the roofing to minimize condensation and maintain air circulation, which is particularly important in greenhouses and storage areas.
Contact Us Today to Purchase Stabilit America’s Corrugated Fiberglass Sheets
Stabilit America’s corrugated fiberglass roofing sheets are available through a network of trusted distributors and retailers. Customizable options, such as lengths up to 24 feet and various colors, ensure that you find the perfect solution for your specific project. For additional information or to request a quote, connect with us through Stabilit America’s customer support team. By selecting Stabilit America’s corrugated fiberglass roofing sheets, you invest in a product that combines durability, performance, and aesthetic appeal. Whether you’re working on a residential, commercial, or agricultural project, these sheets provide reliable protection and functionality for years to come.
FAQs
What are the disadvantages of a fiberglass roof?
Fiberglass roof panels can become brittle over time when constantly exposed to UV rays without protective coatings. While durable, they may not be as flexible as polycarbonate alternatives in certain applications.
How long do fiberglass roof panels last?
With proper installation and maintenance, fiberglass roof panels can last 20–30 years or more, especially when reinforced with protective coatings like those used by Stabilit America.
Which is better, fiberglass or polycarbonate roof panels?
It depends on your application. Fiberglass panels are better for cost-effective, high light-transmitting, and corrosion-resistant applications. Polycarbonate panels offer greater impact resistance and flexibility. Consult with Stabilit Americaabout FRP panels to determine the best fit for your project.
Stabilit America Inc. is a leading North American manufacturer of fiberglass reinforced panels (FRP) and polycarbonate sheets, with over 65 years of experience. The company offers the widest range of acrylic, polyester, and polycarbonate laminates, backed by international certifications (USDA, Greenguard, FM, ISO 9001, among others), serving industries such as industrial construction, transportation, and sustainable building.
Corrosion is a constant challenge across multiple different industries. It can impact the longevity and performance of the materials you use in construction, transportation, and infrastructure. Understanding how corrosion occurs and how to prevent it can help you get long-term durability. While corrosion is usually associated with metal degradation, advances in material science, including FRP from Stabilit America, provide highly effective solutions for applications that demand superior resistance to environmental and chemical exposure.
What Is Corrosion?
Corrosion is considered an electrochemical process that deteriorates different materials. It commonly happens with metal when it interacts with environmental elements such as moisture, oxygen, salts, and industrial chemicals. This degradation can take a few forms, from uniform surface oxidation to deep pitting and structural weakening. While rust is the most recognized form of corrosion, affecting iron and steel, other metals and materials are also susceptible to different types of chemical and environmental breakdown.
At its core, corrosion happens because metals naturally try to achieve a more stable state. Pure metals, especially those higher in the reactivity series, are prone to oxidation, meaning they lose electrons when exposed to air, water, or corrosive substances. Over time, this process weakens the material, compromising structural integrity and requiring costly repairs or replacements.
Factors That Contribute to Corrosion
Several conditions accelerate the rate of corrosion in metal structures and equipment where you might utilize metal parts. Common contributing factors include:
- Environmental Exposure: Continuous contact with oxygen, moisture, and airborne pollutants increases the risk of oxidation and can lead to a gradual surface degradation. Coastal and industrial areas that have high humidity levels and salt content exacerbate the process.
- Chemical Interactions: Exposure to acids, bases, or industrial chemicals weakens protective oxide layers. As a result, this makes metals more vulnerable to corrosion. Processing plants, wastewater facilities, and manufacturing sites have a higher risk level.
- Temperature Fluctuations: High temperatures can accelerate oxidation, while rapid cooling can lead to stress fractures that further expose metals to corrosive agents.
- Structural Design: Crevices, joints, and concealed areas trap moisture and contaminants, creating an environment where corrosion can easily go unnoticed as they develop.
Commonly Affected Materials
While all metals are susceptible to some degree of corrosion, the rate and severity that it happens depend on the composition and environmental exposure.
Metals Prone to Corrosion
Certain metals are more susceptible to corrosion because of their chemical composition and environmental exposure. While some degrade gradually, others can weaken rapidly when exposed to moisture, chemicals, or extreme conditions.
- Iron and Steel: Highly reactive in humid environments, iron and steel form rust when they get exposed to moisture and oxygen.
- Copper and Brass: These materials start to develop patinas over time, especially in marine locations where salt exposure accelerates corrosion.
- Aluminum: Although aluminum is naturally resistant due to its oxide layer, it does corrode in highly acidic or alkaline conditions.
- Zinc: Zinc is often used as a protective coating, but it can degrade over time in aggressive environments.
Corrosion-Resistant Materials
Not all materials corrode at the same rate, and some are designed to resist environmental and chemical damage. Choosing the right option can significantly reduce maintenance costs and structural failures.
- Stainless Steel: Materials like stainless steel contain chromium, which forms a passive layer that prevents oxidation. This property makes it a preferred material for applications requiring long-term durability.
- Titanium: Titanium is very resistant to corrosion, even in high-temperature and aggressive chemical environments.
- FRP (Fiber-Reinforced Plastic): Unlike metal, FRP does not corrode, making it an ideal alternative for environments where long-term exposure to moisture and chemicals is expected.
The Role of FRP in Corrosion Prevention
While traditional metals have been widely used in construction and industrial applications, FRP offers a highly effective alternative for corrosion-prone environments. FRP materials are naturally resistant to moisture, chemicals, and oxidation, making them an excellent choice for structures exposed to harsh conditions.
Unlike metal, FRP does not rely on coatings or galvanization to resist corrosion. Instead, it is engineered to withstand exposure to aggressive environments, reducing the need for maintenance and costly replacements. This advantage makes FRP an increasingly preferred material in applications such as industrial piping, transportation panels, and structural reinforcements where corrosion resistance is a priority.
Types of Corrosion
Different types of corrosion impact materials in various ways. Recognizing these patterns helps in selecting the appropriate materials and preventative measures.
Uniform Corrosion
Occurs evenly across a metal surface due to consistent exposure to air and moisture. While predictable, it weakens materials over time, requiring protective coatings or replacement.
Pitting Corrosion
Manifests as small holes or cavities on a metal surface. This localized damage is dangerous in structural components since it compromises the integrity of your materials, but it isn’t immediately visible.
Crevice Corrosion
Develops in confined spaces where moisture and contaminants get trapped. Areas such as bolts, joints, and metal fittings are extremely susceptible.
Galvanic Corrosion
Happens when two different metals come in contact in a conductive environment, causing one to corrode at an accelerated rate. You usually see this in structures that mix materials like steel and aluminum.
High-Temperature Corrosion
Affects metals exposed to extreme heat, leading to oxidation, sulfidation, or carburization. Power generation and petrochemical processing facilities deal with this type of corrosion most often.
How to Prevent Corrosion
For effective corrosion prevention, you need a combination of proper material selection, protective coatings, and environmental control.
- Choosing Corrosion-Resistant Materials: Stainless steel, titanium, or FRP can extend the lifespan of your structures that are exposed to harsh conditions.
- Protective Coatings: Applying paints, sealants, or galvanization provides an additional layer of defense against oxidation and chemical exposure.
- Regular Maintenance: Routine inspections and cleaning help remove contaminants that accelerate corrosion and prevent long-term damage.
- Proper Drainage and Ventilation: Reducing trapped moisture in structural components helps minimize localized corrosion risks.
- Cathodic Protection: Using sacrificial anodes, including zinc or magnesium, prevents more critical components from corroding.
Investing in Corrosion-Resistant Solutions With Stabilit America FRP Panels
Corrosion is one of the leading causes of material degradation across all industries. It can cause costly repairs, compromised safety, and operational downtime. Choosing the right materials, like FRP panels from our team at Stabilit America, provides superior durability so you can reduce the impact of corrosion on your products. Whether you’re managing industrial infrastructure, transportation, or construction projects, selecting corrosion-resistant materials provides long-term performance, lower maintenance costs, and greater reliability in demanding environments. For more information, explore Stabilit America’s range of corrosion-resistant FRP solutions to enhance durability in your applications.
Stabilit America Inc. is a leading North American manufacturer of fiberglass reinforced panels (FRP) and polycarbonate sheets, with over 65 years of experience. The company offers the widest range of acrylic, polyester, and polycarbonate laminates, backed by international certifications (USDA, Greenguard, FM, ISO 9001, among others), serving industries such as industrial construction, transportation, and sustainable building.
Cooling towers play a critical role in temperature regulation across a wide range of industries. From power generation plants to manufacturing facilities, these systems help to dissipate heat and prevent equipment from overheating and maintain operational efficiency. Selecting the right cooling tower materials requires an understanding of its design, functionality, and material composition. Given the constant exposure to moisture, chemicals, and temperature fluctuations, corrosion-resistant FRP panels from Stabilit America have become the best choice for structural components such as louvers, enclosures, and exterior casing.
How Cooling Towers Work
At their core, cooling towers function as heat rejection systems that work to remove excess heat from industrial processes by evaporating a portion of the circulating water. This process helps lower the temperature of the remaining water, which is then recirculated to absorb more heat from the system.
The efficiency of a cooling tower depends on several factors, including:
- Water circulation rate: The volume of water moving through the system impacts the overall cooling capacity.
- Airflow mechanism: Some cooling towers rely on natural airflow or mechanical fans to facilitate heat exchange.
- Design configuration: Different types of cooling towers optimize cooling performance based on the industry-specific needs of the structure that is being supported.
Cooling towers are effective, but they still require routine maintenance to prevent scaling, biological growth, and efficiency losses. Without proper upkeep, you could see reduced heat transfer, increased energy consumption, and even structural degradation.
Types of Cooling Towers
Cooling towers are classified based on how they facilitate heat transfer. The four primary types include:
1. Natural Draft Cooling Towers
These towers use their height and shape to generate natural airflow, eliminating the need for mechanical fans. You commonly see them used in power plants where they are highly efficient. You should keep in mind that they do require significant space and are costly to construct.
2. Mechanical Draft Cooling Towers
Unlike natural draft designs, mechanical draft towers use fans to force air through the system as a way to increase cooling efficiency. These towers are further divided into two subtypes:
- Forced draft towers push air through the fill media using fans at the base.
- Induced draft towers have fans at the top to pull air upward to optimize heat dissipation.
3. Crossflow Cooling Towers
In a crossflow system, air moves horizontally while water flows vertically through the fill media. These towers allow easier maintenance access and operate with lower energy consumption but can be more prone to freezing in colder climates.
4. Counterflow Cooling Towers
Designed for maximum efficiency, counterflow towers move air in the opposite direction of water flow, increasing the rate of heat exchange. While they require more power for water distribution, they generally provide better cooling performance and are commonly used in industrial applications.
Cooling Towers vs. Chillers: What’s the Difference?
Cooling towers and chillers both manage heat dissipation, but they are not the same thing since they function differently. A cooling tower removes heat from process water through evaporation, making it a good option for industrial applications. On the other hand, a chiller uses refrigerants to absorb and expel heat. They provide precise temperature control in climate-sensitive environments like hospitals and laboratories.
A lot of facilities actually use both systems together, with cooling towers handling large-scale heat rejection and chillers to maintain the cooling temperatures required. The choice between the two depends on factors like energy efficiency, water consumption, and operational requirements.
Key Industries That Rely on Cooling Towers
Cooling towers support a variety of industries by maintaining optimal temperatures for equipment and processes. Some of the most common applications include:
- Power Plants: Essential for steam condensation and waste heat removal in thermal and nuclear power generation.
- Manufacturing Facilities: Regulate temperature in industrial processes such as metal fabrication, plastic molding, and chemical production.
- Data Centers: Prevent overheating of server rooms by efficiently rejecting excess heat.
- Petrochemical and Refining: Support cooling requirements for oil refineries and chemical processing plants.
- HVAC Systems: Provide temperature regulation in commercial buildings, hospitals, and large residential complexes.
Regardless of the application, you need materials for your construction that can withstand extreme conditions to allow for long-term performance.
FRP Panels: Enhancing Cooling Tower Durability
Cooling towers are constantly exposed to moisture, airborne contaminants, and corrosive chemicals. Traditional materials like wood and metal can deteriorate over time, leading to frequent maintenance, costly repairs, and structural instability.
FRP panels provide an advantage through all the hazards that your facility will be exposed to. Designed for corrosion resistance, impact durability, and minimal maintenance, FRP panels are used for louvers, stair enclosures, and exterior casing. Stabilit America’s Opalit Cooling Tower FRP Panels meet the demanding conditions of cooling tower environments, ensuring long-lasting performance with minimal degradation.
Benefits of using FRP panels in cooling towers include:
- They are resistant to chemicals and moisture through the prevention of rusting, rotting, and degradation.
- Our panels create lightweight construction, simplifying the installation and reducing the structural load.
- You get enhanced durability. Our panels maintain their integrity under harsh weather conditions.
- Fire-resistant properties meet industry standards for safety compliance.
By incorporating FRP solutions from Stabilit America, cooling tower systems get greater operational efficiency, lower maintenance costs, and extended service life.
Cooling Tower Maintenance Best Practices
Regular maintenance is important to keep a cooling tower running at peak efficiency. Neglecting upkeep can lead to scale buildup, corrosion, biological contamination, and mechanical failures.
Routine Inspection Checklist
- Check for leaks: Inspect all piping, valves, and structural panels for any signs of deterioration.
- Clean the basin and sump: Remove debris and sediment to prevent clogging and microbial growth.
- Monitor water quality: Test for pH levels, total dissolved solids, and microbial contaminants.
- Inspect fan systems: Make sure all the fans and motors are free of dust buildup and that they are operating at full capacity.
- Evaluate drift eliminators: Replace damaged components to minimize water loss.
Seasonal Maintenance Tips
- Spring Startup: Flush out sediment, inspect nozzles, and verify water distribution systems.
- Summer Operation: Monitor water treatment levels to prevent scaling and corrosion.
- Fall Shutdown: Drain the system, clean components, and apply protective coatings if necessary.
- Winterization: In colder climates, implement freeze protection measures to prevent damage.
Optimize Your Cooling Tower’s Performance With Durable Solutions
Cooling towers are indispensable in industrial and commercial applications, providing reliable heat dissipation. Selecting the right tower type, performing routine maintenance, and utilizing corrosion-resistant materials like FRP panels can improve performance, longevity, and cost efficiency. With an increasing demand for sustainable and energy-efficient cooling solutions, materials from Stabilit America offer long-term advantages in reducing maintenance efforts and improving structural durability. When you’re looking for a reliable, low-maintenance, and high-performance cooling tower solution, integrating FRP-based components is a forward-thinking investment. Contact us today to find out how our products can improve your cooling tower construction.
Stabilit America Inc. is a leading North American manufacturer of fiberglass reinforced panels (FRP) and polycarbonate sheets, with over 65 years of experience. The company offers the widest range of acrylic, polyester, and polycarbonate laminates, backed by international certifications (USDA, Greenguard, FM, ISO 9001, among others), serving industries such as industrial construction, transportation, and sustainable building.