When you think about the elements that define a building’s character, doors might not always come to the forefront of your mind. Yet, these pivotal pieces are more than just entry and exit points. They encapsulate the transition between spaces, embodying both function and form. Door skins help with this, as they subtly elevate a door so it becomes an integral part of a building’s aesthetic and structural integrity.
At Stabilit America, we understand this balance, crafting door skins that stand up to the demands of both nature and use. It’s about ensuring every door does its job beautifully, blending seamlessly into the fabric of your spaces.
What Makes a Door More Than Just a Door?
You may wonder: What is a door skin? Simply put, a door skin is the outermost layer that covers a door’s core, providing both protection and style. It’s what you see first and what shields the door from the harsh realities of daily use. Our door skins are not just any material. They are embossed, reinforced composite panels designed to withstand the elements and the test of time, made with high-quality polyester resins and UV inhibitors.
By providing this additional layer of protection, door skins contribute to the longevity of the door, enhancing its durability and performance while complementing the building’s aesthetic. Whether you’re working in a commercial or residential space, door skins are a practical investment that ensures your doors remain in top condition for years.
The Role of Door Skins in Construction
When it comes to construction and remodeling, every detail counts—right down to the choice of door skins. Whether it’s a bustling hospital corridor, a classroom full of eager learners, or a robust agricultural facility, all door skins are tailored to meet diverse requirements, reinforcing doors where it matters most.
- Durability: Door skins protect against wear and tear, ensuring doors withstand the daily hustle and bustle.
- Resistance: They offer a shield against environmental challenges like rust, corrosion, and moisture.
- Aesthetics: Beyond functionality, door skins provide a canvas for design, allowing doors to complement or elevate a space’s overall look.
- Customization: With a variety of materials and finishes available, door skins can be customized to meet specific needs, such as enhanced hygiene in healthcare settings or increased insulation in cold storage units.
- Ease of Maintenance: Designed for easy cleaning and upkeep, door skins help maintain hygiene standards and aesthetic appeal without requiring excessive effort.
As you navigate your next project, remember that the right door skin can significantly impact a building’s functionality and aesthetic. It’s about making informed choices that contribute to the longevity and performance of your doors, ensuring they remain an asset rather than a maintenance burden.
Choosing the Right Door Skin for Your Project
Selecting the right door skin for your project is a nuanced decision influenced by a variety of factors that go beyond mere appearance. This choice can dictate not only the longevity and resilience of your doors but also how they integrate with the building’s overall aesthetic and functional requirements. It’s a decision that merits careful consideration tailored to the specific demands of your project.
- Material Compatibility: Ensure the door skin material complements the core door material for optimal performance and durability.
- Environmental Conditions: Choose materials that can withstand the specific conditions they’ll face, whether it’s high humidity, extreme temperatures, or direct sunlight.
- Design and Aesthetics: Look for door skins that align with your project’s aesthetic vision, offering the right color, texture, and finish.
- Maintenance Requirements: Consider how easy the door skin is to clean and maintain, especially in high-traffic areas.
- Safety and Compliance: Make sure your choice meets all relevant safety standards and building codes, especially for fire resistance.
- Budget Constraints: Balance quality with cost, aiming for the best value that meets both your aesthetic and functional needs without compromising on quality.
Making the right selection involves weighing these factors carefully, ensuring that your doors not only look the part but also stand up to the rigors of their intended use. The right door skin enhances both the form and function of a door, contributing to a project’s success on multiple levels. Remember, a well-chosen door skin is an investment in the longevity and aesthetic appeal of your space, making it a detail worth getting right.
Advantages of Integrating Door Skins into Your Buildings
Integrating door skins into your buildings offers a multitude of benefits that can significantly enhance both the functionality and aesthetic appeal of your doors. From bolstering durability to expanding design possibilities, the advantages are compelling and worth exploring for any construction or remodeling project.
- Enhanced Durability: Door skins add a protective layer that guards against daily wear and tear, ensuring doors remain in top condition for longer.
- Aesthetic Versatility: With a wide range of designs and finishes available, door skins make it possible to match any architectural style, whether you’re aiming for a modern look or a traditional feel.
- Ease of Installation: Designed for quick and straightforward application, door skins can save valuable time on the construction site, streamlining the installation process.
- Cost-Effectiveness: By extending the life of doors and reducing the need for frequent replacements or repairs, door skins offer a cost-efficient solution in the long run.
- Improved Resistance: They provide an additional layer of defense against environmental factors such as moisture, temperature changes, and even UV exposure, depending on the material chosen.
- Low Maintenance: Once installed, door skins require minimal upkeep, making them a practical choice for busy environments.
Choosing door skins for your project is a smart move that can elevate the quality and appearance of your doors. It’s a decision that not only reflects a commitment to durability and design but also enhances the overall value of your building. With these benefits in mind, it becomes clear why door skins are an increasingly popular choice among architects and builders aiming for excellence in their projects.
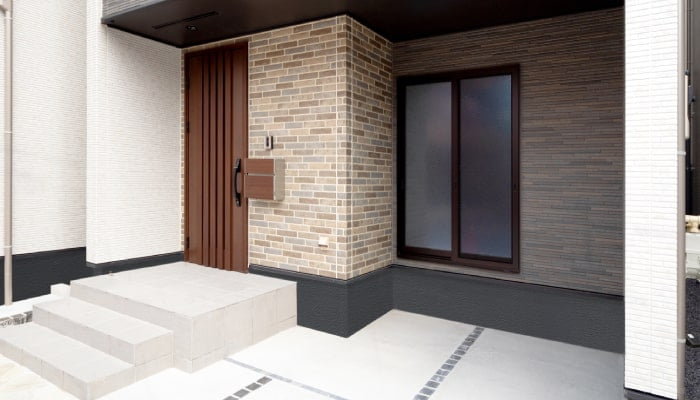
Elevate Your Project With the Right Door Skins
Grasping the full scope of what is a door skin can profoundly impact the effectiveness and aesthetic appeal of your construction or remodeling projects. By integrating the right door skins, you ensure your doors not only meet the functional demands but also enhance the visual harmony of your spaces. Contact us to explore our door skins, tailor-made to suit diverse architectural needs and stylistic preferences. Take the next step toward elevating your projects with door skins that promise quality, durability, and style.
FAQs
What is the purpose of door skins?
Door skins serve as the outer protective layer of a door, offering both structural protection and aesthetic enhancement. They shield the core of the door from wear and tear, environmental damage, and moisture, ensuring longevity while contributing to the visual appeal of the space.
How do door skins differ from traditional doors?
Door skins are an external layer that covers the core of a door, often made from durable, impact-resistant materials. In contrast, traditional doors are often a single solid piece. Door skins provide an added layer of customization, protection, and longevity to the basic door structure.
What materials are used for door skins?
Door skins are commonly made from high-quality polyester resins, fiberglass, metal, and other composite materials that provide excellent durability, moisture resistance, and aesthetic flexibility. These materials help protect the door from physical and environmental damage, ensuring it lasts for years.
Stabilit America Inc. is a leading North American manufacturer of fiberglass reinforced panels (FRP) and polycarbonate sheets, with over 65 years of experience. The company offers the widest range of acrylic, polyester, and polycarbonate laminates, backed by international certifications (USDA, Greenguard, FM, ISO 9001, among others), serving industries such as industrial construction, transportation, and sustainable building.
Building a greenhouse is a big task. It requires careful consideration of multiple factors to ensure success. Perhaps one of the most important decisions you’ll have to make is the choice of material for the covering. There are several options available when it comes to materials. Yet one of these materials truly stands out: polycarbonate. What is most remarkable about polycarbonate is its durability, light transmission properties, and insulation capabilities.
However, what many people want to know when working with this modern material is “how thick should polycarbonate be for a greenhouse to perform the best?” This comprehensive guide will get into this question, hoping to give you the knowledge you need to make the best decision.
Understanding Polycarbonate
Before we get into the details of thickness, it’s important to understand what polycarbonate is and why it’s a popular choice for greenhouses. Polycarbonate is a type of plastic that is incredibly durable and resistant to both high and low temperatures. It’s a thermoplastic, meaning it can be heated and cooled repeatedly without losing its shape or properties. This makes it an ideal material for environments that experience significant temperature fluctuations—think about how a greenhouse could be exposed to cold in the morning and night, but then get very warm from the sunlight at noon!
Polycarbonate is also known for its ability to transmit light. Because light is necessary for plant growth, this is a key feature for building greenhouses. Polycarbonate allows the majority of the sun’s light to pass through while blocking harmful UV rays. Think about how happy your plants or crops will be with all the light they need, but without the risk of damage from overexposure to UV radiation!
Because different greenhouses face different environments and climate conditions depending on their geographic location, one size does not fit all. There need to be different polycarbonate thickness options that can perform well in the different situations. This is why, in every project, you will come to a point where you ask yourself: how thick should polycarbonate be for a greenhouse like mine?
Fortunately, polycarbonate panels come in different thicknesses, typically ranging from 4mm to 25mm. The thickness you choose will significantly impact the insulation, strength, and cost of your greenhouse. With such a wide range of thicknesses, you are sure to find a polycarbonate sheet that truly fits your project well.
Insulation and Light Transmission
If you are building a greenhouse, it’s because you want to create a controlled environment where heat and light can be managed effectively. The thickness of the polycarbonate plays a crucial role in this aspect.
Thicker polycarbonate panels have better insulation properties, which means your space will retain heat more effectively. This becomes very important in colder climates where maintaining a warm temperature inside the greenhouse can be difficult—greenhouses in some parts of the world face temperatures well below zero. The insulating property of polycarbonate is due to the multiwall structure of the panels, which creates air pockets that trap heat. As the thickness increases, so does the number of these air pockets, leading to better insulation. This is the same principle that works in down jackets: what keeps you warm is all the air between the feathers.
A common misconception is that thicker panels will reduce light transmission. People get afraid that with thicker panels, their plants or crops won’t be able to grow. However, polycarbonate panels, regardless of their thickness, have excellent light transmission properties. Even a 25mm thick panel can transmit over 80% of light, which is more than enough for most plants! The diffused light provided by polycarbonate panels also helps to prevent plant burn and ensure that light reaches all parts of the plant, not just the top. This soft diffused light coming from all directions is not only beneficial for plants, but it creates a really pleasant environment for humans too!
Strength and Durability
The thickness of the polycarbonate also impacts the strength and durability of the greenhouse. Thicker panels are more rigid and can withstand harsh weather conditions better than thinner ones. This becomes more and more important as the climate is becoming more extreme lately. Thicker polycarbonate sheets are less likely to crack or break due to hail, wind, or snow loads. You want to make sure to consider this if you live in an area prone to severe weather, as damage to the greenhouse can lead to significant losses.
In addition to weather resistance, thicker polycarbonate panels also offer better resistance to physical damage. Whether it’s an errant football from a neighborhood game or a fallen tree branch, thicker panels are more likely to withstand the impact without breaking. This can save you the cost and hassle of frequent replacements.
Cost Considerations
While thicker polycarbonate panels offer better insulation and durability, they also come with a higher price tag. Therefore, it’s essential to balance the benefits of thicker panels with your budget constraints. A well-constructed greenhouse with thinner panels can still provide excellent results if managed correctly. It is all about getting the right type of panels for your situation.
The cost of polycarbonate panels is not just the upfront purchase price. You should also consider the long-term costs, such as heating costs in winter. Thicker panels, with their better insulation, can significantly reduce these costs, making them a more economical choice in the long run.
So, What’s the Ideal Thickness?
When you are considering how thick should polycarbonate be for a greenhouse, strike a balance between budget, potential forces that your greenhouse will endure, and temperature considerations. You may live in a warmer climate where heating is not a concern, but strong winds may be. Think about the entire year and what kind of weather conditions your greenhouse will face, in addition to neighbors, and impact risks that may come from them.
The “ideal” thickness of polycarbonate for a greenhouse largely depends on your specific needs and circumstances. If you live in a colder climate and need superior insulation, or if your area is prone to harsh weather conditions, opting for thicker panels (8mm or more) would be beneficial. However, if you live in a milder climate and are working with a tight budget, thinner panels (around 4-6mm) could suffice.
It’s also important to consider the types of plants you plan to grow. Some plants require more heat and light than others, and the thickness of the polycarbonate can impact these conditions.
Conclusion
Choosing the right thickness of polycarbonate for your greenhouse is a decision that should be based on your climate, budget, surroundings, and specific plant needs. While thicker panels offer better insulation and durability, they also come at a higher cost. Therefore, it’s essential to evaluate your specific needs and make a decision that offers the best balance between performance and cost.
In the end, the goal is to create a space where your plants can thrive, and the right polycarbonate thickness is a significant step towards achieving that goal. With careful consideration and planning, you can build a greenhouse that not only meets your needs but also provides a rewarding experience.
Stabilit products for Greenhouse Applications
Acrylit by Stabilit offers quality corrugated acrylic roof panels available in multiple colors and profiles. They are proven to last over 20 years, with a 10-year warranty against yellowing and delamination. The Acrilyt High Impact line has excellent resistance against inclement weather conditions.
Stabilit America’s Macrolux Rooflite corrugated panels, fabricated with high-tech Macrolux polycarbonate resin, are a durable and versatile choice for various outdoor applications, including greenhouses. These lightweight panels are designed to withstand extreme weather conditions, including hail damage and surface erosion, while also offering UV protection.
Stabilit has a material that fits your needs. Contact us y and find out more about how we can help!
FAQs
What is the purpose of louvers?
Louvers are architectural elements designed to allow for ventilation and natural light while protecting a building from the entry of water and debris. They are commonly used in facades, roofs, and windows to provide air circulation, reduce energy consumption, and enhance the building’s aesthetics.
What is the difference between a louver and a vent?
While both louvers and vents allow for airflow, louvers have adjustable slats or blades designed to control the direction and amount of air entering a space, offering better protection against the elements, such as rain. Vents, on the other hand, are simple openings without the same level of control over airflow.
What is the difference between louvre and louver?
“Louvre” is the traditional spelling used in British English, while “louver” is the Americanized version. Both terms refer to the same architectural feature, though the spelling may differ depending on the region.
Stabilit America Inc. is a leading North American manufacturer of fiberglass reinforced panels (FRP) and polycarbonate sheets, with over 65 years of experience. The company offers the widest range of acrylic, polyester, and polycarbonate laminates, backed by international certifications (USDA, Greenguard, FM, ISO 9001, among others), serving industries such as industrial construction, transportation, and sustainable building.
Elevate the appeal and functionality of your mobile eatery with Stabilit America’s FRP panels, designed specifically for food trucks. These innovative interior FRP wall trailer panels offer a lightweight yet robust solution that revolutionizes your food truck’s interior. Step into the future of food service where hygiene, aesthetics, and practicality blend seamlessly, thanks to the ease of installation, weight reduction, and exceptional resistance to humidity provided by our FRP panels. Embark on the journey of transforming your food truck into a paragon of high-quality culinary space.
The Benefits of FRP Panels in Food Truck Construction
Embracing innovation in food truck construction is pivotal, and FRP panels in food trucks are the cornerstone of this modern approach. Designed to support the vigor of mobile cuisine without the burden, these panels offer the ideal balance between durability and practicality.
Enhanced Structural Integrity with Lightweight Design
The genius of FRP panels lies in their high strength-to-weight ratio. In the bustling world of food trucks, where every pound matters, these panels maintain structural integrity without adding excessive weight to your vehicle. This means easier maneuverability on the streets and less wear on your vehicle over time. Plus, the rigid composition of FRP panels guards against dents and damage that are all too common in a high-traffic kitchen, ensuring that your investment retains its form and function even through the rigors of road travel and frequent service.
Ease of Cleaning and Maintenance
In the realm of food service, cleanliness is not just a necessity—it’s the law. FRP panels rise to the challenge with a non-porous surface that’s a breeze to clean, requiring nothing more than a simple wipe-down to keep it looking pristine. Unlike other materials that can harbor bacteria and odors, FRP stands as a stalwart against spills and stains. This ease of maintenance means more time serving customers and less time scrubbing walls, optimizing your operations and ensuring that your food truck remains a beacon of hygiene in the fast-paced food industry.
With Stabilit America’s FRP panels, upgrading your food truck goes beyond an aesthetic makeover—it’s an investment in your business’s efficiency and longevity. These panels empower you to sail through health inspections and sustain the demands of daily operations with ease. Choose FRP panels for a food truck that’s as robust in its build as it is in its culinary offerings.
Safety and Sanitation with FRP Panels for Food Trucks
When it comes to food trucks, where every serving space is precious, FRP panels emerge as the hygienic champion. Let’s delve into the features that make these panels an essential part of maintaining food safety and cleanliness on the move.
Non-Porous Surface for Hygienic Prep Areas
The non-porous nature of FRP panels stands as the first line of defense in your food truck’s battle against bacteria and contamination. Unlike traditional materials that can absorb moisture and harbor pathogens, these panels provide no refuge for microbes, ensuring that your preparation area remains uncontaminated. This quality is particularly invaluable in the tight confines of a food truck, where efficient use of space must coincide with stringent hygiene practices.
Meeting Food Safety Standards
FRP panels are not only easy to clean but are designed to meet the rigorous food safety standards required in the food service industry. They contribute to a cleaner cooking environment by resisting the accumulation of grime and grease, which are inevitable in the kitchen. Compliance with health codes becomes less of a hurdle and more of a natural outcome of choosing materials that are tailored for food safety.
Incorporating FRP panels into your food truck is a smart move that pays off in cleanliness and peace of mind. The ease of sanitizing these surfaces means that you can focus on what you do best—creating delicious food for your customers—while trusting that your workspace remains pristine. With Stablit America, step into a cleaner, safer future where your food truck leads the way in both taste and hygiene standards.
Efficiency and Functionality Enhanced by FRP Panels
In the bustling world of food truck businesses, speed and efficiency are as crucial as the flavor of the dishes served. FRP panels are a game-changer, providing solutions that streamline the setup and maintenance of your mobile kitchen.
Accelerated Installation Process
The quick installation of FRP panels is a boon for food truck operators eager to hit the road. Unlike traditional materials that require extensive time for fitting and curing, FRP panels can be installed in a fraction of the time. This means your food truck can transition from concept to serving customers much faster, maximizing your business days and revenue potential. The simplicity of the installation process also means that renovations or repairs can be accomplished with minimal downtime, keeping your culinary show on the road.
Durability and Low Maintenance
Durability is not just about withstanding the test of time—it’s about enduring the daily rigors of a high-energy kitchen. FRP panels boast a resilience that stands up to the constant opening and closing of service windows, the bumps and knocks of kitchen activity, and the frequent cleaning that food service areas require. This toughness translates to fewer repairs and replacements. Moreover, the easy-to-clean nature of FRP panels means less time spent on maintenance and more on customer satisfaction, enhancing the truck’s overall operational efficiency.
By choosing FRP panels for your food truck, you’re investing in more than just the material—you’re investing in an efficient, robust platform for your culinary endeavors. Stablit America takes pride in offering products that not only streamline the start-up process but also support the ongoing success of your mobile business. Embrace FRP panels and let your food truck set the pace in a competitive market where efficiency is not just desired but deliciously achieved.
Embrace the Journey with Stabilit America’s FRP Panels
It’s time to rev up your food truck’s potential with Stablit America’s FRP panels. Seize the opportunity to streamline your operations, embrace durability, and ensure a seamless service experience. Let each meal you craft be backed by the confidence of a well-equipped, efficiently designed truck. Contact us today to equip your mobile venture with FRP panels and turn the key to a future where quality, speed, and hygiene drive your road to success.
FAQs
What are the benefits of FRP panels for food trucks?
FRP panels offer numerous benefits for food trucks, including lightweight design, ease of cleaning, and exceptional resistance to humidity. These panels contribute to a hygienic environment, ensuring that food safety standards are met while enhancing the aesthetic appeal and functionality of the truck.
Are FRP panels easy to install in food trucks?
Yes, FRP panels are designed for easy installation, significantly reducing the time required for setup. This means that food truck operators can hit the road faster and spend less time on renovations and repairs.
How do FRP panels for food trucks compare to other materials?
Unlike traditional materials, FRP panels are non-porous, resistant to corrosion, and much easier to clean, making them a superior choice for maintaining hygiene in food trucks. Additionally, they are more durable and provide better insulation compared to materials like wood or metal.
Stabilit America Inc. is a leading North American manufacturer of fiberglass reinforced panels (FRP) and polycarbonate sheets, with over 65 years of experience. The company offers the widest range of acrylic, polyester, and polycarbonate laminates, backed by international certifications (USDA, Greenguard, FM, ISO 9001, among others), serving industries such as industrial construction, transportation, and sustainable building.
In the ever-evolving world of construction and architectural design, every element plays a crucial role in the functionality and aesthetic appeal of a building. Louvers, often overlooked, are such elements that significantly impact both. But what are louvers, and how do they integrate into modern architecture? This article delves into the essence of louvers, their benefits in commercial buildings, and guidance on selecting the right type for your project—with a nod to the innovative solutions provided by Stabilit America
What Are Louvers and Their Role in Modern Architecture?
Louvers are architectural staples that marry function with form in modern design, allowing buildings to breathe and bathe in natural light while shielding interiors from water and debris. Crafted from materials like aluminum, metal, wood, and Fiberglass Reinforced Panels (FRP), they are seamlessly integrated into building facades, roofs, and windows, enhancing both utility and aesthetics.
Their role is crucial in modern architecture, offering a smart solution to achieve well-ventilated, luminous spaces that are protected from the elements. With Stabilit America’s FRP options, louvers not only contribute to a building’s efficiency and comfort but also add a layer of design sophistication, ensuring every project stands out for its functionality and visual appeal.
Benefits of Using Louvers in Commercial Building Designs
The strategic incorporation of louvers into commercial buildings will bring you many functional enhancements that don’t just help with the aesthetic appeal of your building. These elements can really transform the way structures interact with their surroundings.
Enhanced Ventilation
The design of louvers allows for the optimal flow of natural air, diminishing the building’s dependence on mechanical ventilation systems. This natural ventilation supports a healthier indoor atmosphere, reducing the accumulation of pollutants and contributing to the well-being of occupants.
Improved Energy Efficiency
Louvers serve as a gateway for natural illumination, minimizing the reliance on artificial lighting during daylight hours. This not only lowers energy consumption but also enhances the mood and productivity of those within the space, making buildings greener and more cost-effective to operate.
Increased Privacy and Security
The strategic placement of louvers offers a clever solution to privacy concerns, as they allow for the passage of light and air while shielding the interior from external observation. This feature is especially valuable in urban settings, where buildings are in close proximity to each other.
Weather Protection
Engineered to deflect water and resist environmental elements, louvers add an extra layer of protection against the weather. Their ability to prevent rainwater ingress safeguards the interior from potential water damage, ensuring the longevity and durability of the building fabric.
The integration of louvers into commercial structures addresses a broad spectrum of architectural challenges, from enhancing occupant comfort to promoting energy efficiency and safeguarding privacy. With Stabilit America’s expertise in Fiberglass Reinforced Panels, selecting louvers for your next project means investing in a solution that offers both form and function, ensuring your building is equipped to meet the demands of modern architecture.
Choosing the Right Louver for Your Construction Project
Selecting the perfect louver for your construction project isn’t just about aesthetics—it’s a critical decision that impacts the functionality and performance of your building. With a myriad of options available, understanding the key factors that influence this choice can make all the difference.
Environmental Conditions
The climate in the area where you are building your structure needs careful consideration and will affect what you do when you are choosing louvers. In areas that are prone to high winds, selecting louvers designed to withstand these kinds of forces is extremely important and will help prevent damage and maintain ventilation efficiency. Similarly, for buildings in regions with frequent rainfall, water-resistant louvers ensure that moisture does not compromise the interior spaces. Solar exposure is another vital factor; louvers with sun-deflecting capabilities can significantly reduce cooling costs and enhance occupant comfort.
Architectural Aesthetics
Louvers are an integral part of your building’s visual identity. FRP louvers offer unmatched flexibility in design, allowing for a seamless integration with any architectural style. Whether your project calls for a modern, sleek appearance or a more traditional look, the ability to custom fabricate FRP louvers means there’s no need to compromise on aesthetics. Their versatility ensures that the final design will not only meet your functional requirements but also elevate the building’s overall appeal.
Functionality
The operational demands of your project dictate the functionality needed from your louvers. Adjustable louvers provide the flexibility to control airflow and light penetration, adapting to varying conditions and occupant needs. For projects where noise reduction is a priority, louvers with acoustic-dampening features can contribute to a quieter, more serene environment. Additionally, in settings where safety is paramount, opting for louvers with fire-resistant properties adds an extra layer of protection, ensuring peace of mind for both occupants and owners.
Stabilit America’s FRP Louvers offer a versatile solution, blending durability with design flexibility. These louvers provide excellent corrosion resistance, making them ideal for industrial and commercial applications where air intake and exhaust are critical concerns. Whether you need center pivot adjustable blade louvers or stationary ones, Stabilit America custom fabricates to any size opening, ensuring a perfect fit for your project’s specific needs.
Integrating Louvers Into Your Next Project With Stabilit America
Louvers are much more than just architectural accents. They are essential components that contribute to the operational efficiency and visual appeal of a building. By choosing Stabilit America for your louver needs, you tap into a wealth of expertise in FRP manufacturing, gaining access to products that promise longevity, performance, and style.
As you plan your next construction project, consider how louvers can enhance your structure. From improving energy efficiency to adding a layer of protection against the elements, the right louvers can make a significant difference. Check out all construction accessories in our inventory to find the perfect louver solutions for your building, and contact us for expert advice on making the best selection.
FAQs
What is the purpose of louvers?
Louvers are architectural elements designed to allow for ventilation and natural light while protecting a building from the entry of water and debris. They are commonly used in facades, roofs, and windows to provide air circulation, reduce energy consumption, and enhance the building’s aesthetics.
What is the difference between a louver and a vent?
While both louvers and vents allow for airflow, louvers have adjustable slats or blades designed to control the direction and amount of air entering a space, offering better protection against the elements, such as rain. Vents, on the other hand, are simple openings without the same level of control over airflow.
What is the difference between louvre and louver?
“Louvre” is the traditional spelling used in British English, while “louver” is the Americanized version. Both terms refer to the same architectural feature, though the spelling may differ depending on the region.
Stabilit America Inc. is a leading North American manufacturer of fiberglass reinforced panels (FRP) and polycarbonate sheets, with over 65 years of experience. The company offers the widest range of acrylic, polyester, and polycarbonate laminates, backed by international certifications (USDA, Greenguard, FM, ISO 9001, among others), serving industries such as industrial construction, transportation, and sustainable building.
Temperature changes, different types of climates, pollution, and sunshine are some of the factors that have an effect on man-made structures. This leads to phenomena such as cracks, abrasion, sinking, breakdown, and deformation. Additionally, other effects can show up in structures, such as efflorescence and delamination. Often, and concerningly so, degradation or breakdown symptoms can appear. When this happens, materials are not recoverable. This makes you wonder: exactly what does “corrosion resistant” mean?
What is corrosion resistance?
Most structures are planned and erected with long-term use in mind. Because of this, the conditions they will face need to be considered and planned for, especially if they are commonplace, such as weather, pollution, and sunlight. This consideration and planning leads to actions intended to prevent wear, prolong useful life, and limit service interruptions due to maintenance. A fundamental step in this direction is choosing the right materials from the beginning. Given that wear and degradation due to chemical or electrochemical reactions is common, it is important to be very clear on what exactly corrosion resistance means, so that we can select a product that truly performs as we need it to.
To understand how certain materials are able to prevent corrosion and the importance of preventing it, we must be clear on what it is. Corrosion is the deterioration of materials as a result of chemical and electrochemical reactions. Corrosion as deterioration or wear usually refers to metals, because when it comes to ceramics and polymers, it is called degradation.
Corrosion is a natural phenomenon that is influenced by the material that undergoes deterioration, the environment, and, frequently, water. It is also possible to find other substances that can cause corrosion. These are called corrosive substances, and some of them include:
- Perchloric acid
- Nitric acid
- Sulphuric acid
- Chlorhydric acid
- Formic acid
The speed at which corrosion sets in depends on the factors involved. Regardless of the reasons that apply in each case, material deterioration due to electrochemical reactions is a concern for those involved in the construction industry, as it causes damage and financial losses.
Types of corrosion
There are several ways to classify corrosion, but there is one approach that is the most comprehensive, because it contains all possible kinds of corrosion. Dividing corrosion into chemical and electrochemical allows us to classify deterioration according to types of materials and the reaction taking place.
- Chemical: This form of corrosion takes place when a material reacts to a corrosive substance until it is either dissolved or it saturates the material. This classification includes chemical attack, selective lixiviation, and chemical metal attack.
- Electrochemical: Occurs when there is a loss of electrons from atoms, turning them into ions. This category contains galvanic, microbiological and superficial aeration corrosion.
Is corrosion the same as oxidation?
Oxidation and corrosion are not the same; although oxidation does cause a change in materials, it is just a superficial reaction. It occurs when oxygen comes in contact with other substances, such as metals. In the case of metals, brown discolored spots can be observed. This is oxide.
Because oxidation happens only on the surface, it can be removed, as opposed to corrosion, which implies a structural deterioration. In some cases, oxidation is considered a precursor to corrosion. Steps should be taken to control the former, in order to prevent the latter. Damage from corrosion is irreparable.
Corrosion resistance
The term refers to the capacity some materials have to resist the damage that can result from coming in contact with other substances or the environment.
Corrosion resistance can be a property of a material, or can be attained by adding another substance to the product. This additional substance may bring forth the desired resistance. Such is the case with metals that frequently rely on coatings, alloys or paints that can delay or completely prevent corrosion.
Are Stabilit products corrosion resistant?
One of the simplest solutions to avoid corrosion and prevent maintenance costs in any structure is to use materials designed with anticorrosive qualities. Of course, Stabilit manufactures laminated plastics considered corrosion-resistant. They are designed to provide engineers, architects, builders, contractors, and property owners a modern solution, reinforced with fiberglass, to meet their needs. FRP panels like those manufactured by Stabilit offer superior corrosion resistance, performance, and versatility.
Resolite
The Resolite brand includes products composed with polyester, which boosts corrosion resistance. This was our first product line to include a fire retardant option (Resolite CR) in its lineup of plastic laminates.
Resolite provides multiple options so that any building or structure can succeed at meeting its requirements. Resolite CR-RFM is a strong opaque laminate that meets the Factory Mutual standards for fire resistance and wind resilience.
Resolite (RFM) is produced using a high-quality polyester resin system with a protective barrier that binds with the resin and fiberglass matrix. The result is a panel much more protected against degradation and with great durability.
Opalit
Another anticorrosive polyester sheet that is part of the Stabilit America product line is Opalit. In the last decade several new materials have been developed that can fulfill performance requirements similar to metallic laminates, but with none of their downsides. Opalit is such a product.
Opalit for Cooling towers can handle the extremely corrosive environments of cooling towers. It is designed specifically for use in louvers, stair enclosures and exterior casings. Opalit for Agricultural applications is engineered to withstand the ammonia gasses from chickens and pig waste. This makes it ideally suited for roofing and ceilings in poultry and hog farms. It is strong and durable, while also aesthetically pleasing. Its Gelcoat finish protects against UV rays, humidity and pollution, while preventing the dreaded fiber bloom and aging that plagues other brands. There is a fire-retardant option available as well.
Key Benefits of Stabilit FRP
Because they are so strong, FRP sheets can last over 20 years and are highly resistant to corrosion and humidity. Here are some key benefits when compared to metal sheets:
- Cost savings
- Strength and mechanical resistance
- Low thermal conductivity
- Design flexibility
- Longer useful life
- Better surface finish
- Electrical insulation properties
- Vibration reduction and noise dampening
- Lighter by 40 to 50%
- Flexibility
- Corrosion resistance
- Minimal maintenance
- Impact resistance
- Resists the elements, acids, and humidity
If you want to know more about corrosion-resistant materials for the industrial and agro-industrial sectors, you need to dive into fiberglass-reinforced plastics. Visit our page “What is FRP?” to learn more about this. When building any structure, it is better to anticipate maintenance costs and choose the best, high-quality construction materials.
Stabilit America: technology, strength, quality, and aesthetics for every one of your projects
At Stabilit America we produce and distribute materials that truly support your success. For construction, remodeling or even transportation projects, our quality and technological innovations deliver results. Whether you want strength, durability, a better cost-benefit ratio, light transmission, compatibility, thermal insulation or UV protection, we have the key material to get you where you are trying to go.
We manufacture fiberglass-reinforced polymer panels and polycarbonate sheets that can integrate effectively into any modern construction project. They provide benefits such as UV protection or microbe resistance, depending on the needs of your project. Which of our solutions is the best fit for your needs?
Acrylit
Glasliner
Macrolux Multiwall
Macrolux Rooflite
Macrolux Solid
Macrolux AM
Opalit
Resolite CR
Polylit
Acryloy CR
Versalit
Interior and exterior walls, roofs, covers, skylights, canopies, luggage and cargo boxes, truck walls… for any industrial, institutional, commercial or transportation project, Stabilit has a material that fits your needs. Contact us and find out more about how we can help!
FAQs
What does corrosion-resistant mean in construction?
It refers to a material’s ability to withstand environmental or chemical exposure without degrading over time, ensuring longevity and reduced maintenance.
What types of materials are corrosion-resistant?
FRP panels, stainless steel, aluminum with protective coatings, and polymer composites are among the most effective corrosion-resistant materials.
Why should I choose FRP panels over metal sheets?
FRP panels offer better corrosion resistance, require less maintenance, and are lighter and easier to install. They are also more adaptable to harsh environments.
Where can I buy corrosion-resistant FRP panels?
You can explore and purchase FRP panel solutions directly through Stabilit America or contact our team to receive tailored guidance.
Stabilit America Inc. is a leading North American manufacturer of fiberglass reinforced panels (FRP) and polycarbonate sheets, with over 65 years of experience. The company offers the widest range of acrylic, polyester, and polycarbonate laminates, backed by international certifications (USDA, Greenguard, FM, ISO 9001, among others), serving industries such as industrial construction, transportation, and sustainable building.
Over sixty years ago, Stabilit America started on a mission to transform the building materials industry through the innovative use of fiber-reinforced plastics (FRP). Over the decades, this mission has guided us from a humble beginning to becoming a global leader in composite solutions. With each new product and innovative feature, we have paved the way for transportation, commercial, and industrial design solutions. Learn more about Stabilit America by following how we came to where we are now.
1959: The Foundation
Our journey first began when Stabilit America was established with a vision to innovate within the plastic panel and sheet sector. From that point, we quickly distinguished ourselves by mastering the production of fiberglass-reinforced plastic sheets, laying the groundwork for all of our future advancements. This early focus on specialized production allowed us to lay a solid foundation in material technology, influencing how structures and spaces are designed and built today.
1993: Expansion into Monterrey
An extremely important moment in Stabilit America’s history was when we opened a new production plant in Monterrey, Mexico. This expansion increased our overall manufacturing capabilities and marked the beginning of our presence in the international market. The Monterrey plant scaled our operations to astounding new levels and also brought us closer to key markets. As a result, this allowed for faster delivery and better customer service.
1997–2001: Strategic Acquisitions
The late 90s and early 2000s were a period of rapid growth for Stabilit America. This period in our history was marked by key acquisitions, including Glasteel in Tennessee, USA (1997) and the subsequent integration of Resolite and Graham in California, USA (2001). These acquisitions helped expand our product range and their technological edge in the industry. We carefully selected each and every acquisition to make sure it would complement our existing capabilities and broaden our reach across various sectors, allowing us to continue to lead in innovation and service.
2000: Establishing Stabilit Europe
In a move to cement our global presence, Stabilit America set up Stabilit Europe in Barcelona, Spain. This marked a huge step in our strategy to serve the European market directly, enhancing their global distribution channels. By establishing a foothold in Europe, we have been able to expand our market reach while enriching our understanding of diverse architectural needs and preferences. As we continue to grow globally, we remain dedicated to supporting your architectural ambitions with globally recognized and trusted building solutions.
2016: Technological Advancements in Monterrey
The introduction of a discontinuous production line in Monterrey in 2016 exemplified Stabilit America’s commitment to technological innovation. This advancement allowed for improved production efficiency and product quality, meeting the increasing demands of modern construction projects. This innovative approach streamlined our manufacturing processes and helped us make sure we could always provide our customers like you with high-quality materials tailored to meet specific project requirements. As we continue to embrace cutting-edge technologies, we’re ready to support your construction ambitions with materials that set industry standards for excellence and reliability.
2017: Global Expansion Continues
The acquisition of Koscon in Switzerland, later renamed Stabilit Suisse, further demonstrated Stabilit America’s commitment to global expansion. This strategic move bolstered our European market presence and brought new technologies into our manufacturing processes. By integrating these advanced technologies, we have enhanced our capability to offer innovative and sustainable building solutions that address your unique challenges. This expansion also reflects our ongoing effort to bring you globally competitive products and services, ensuring that your projects benefit from the latest advancements in building material technology.
Today and Beyond
Now, Stabilit America continues to lead in the industry with a focus on sustainability, innovation, and quality. Our products, including the acclaimed Polycarbonate Multiwall and Acrylit panels, are recognized for their light transmission, energy savings, and environmental benefits.
Innovations in Building Materials
Stabilit America has consistently been at the forefront of the building materials industry, redefining the standards of construction and design with innovative solutions. All of your projects benefit from materials that always meet the highest quality standards and push the boundaries of functionality and aesthetics:
- Technological Pioneering: Stabilit America was among the first to utilize polycarbonate and FRP technologies to develop products that offer superior durability and performance. Our groundbreaking work has set new benchmarks in the industry for light transmission and impact resistance, making your construction projects safer and more energy-efficient.
- Custom Solutions: Recognizing that no two projects are the same, we have continued to master the art of providing tailor-made solutions that fit the needs of your projects. Whether it’s custom colors, finishes, or profiles, we provide you with materials that enhance your overall design.
- Sustainable Practices: With a strong commitment to sustainability, Stabilit America’s products contribute to LEED credits, helping you build not just for today but for a sustainable future. Our innovations in eco-friendly materials have helped so many projects reduce their environmental footprint while maintaining high standards of quality and durability.
Mission and Vision
Stabilit America has carved a niche in the building materials industry with a clear mission to enhance architectural possibilities through innovative and durable solutions. Our company’s vision is rooted in sustainability and excellence, aiming to push the boundaries of what building materials can achieve in terms of functionality and environmental responsibility. Stabilit is committed to delivering products that exceed customer expectations, emphasizing durability, versatility, and ecological sensitivity. Through advanced technology and a commitment to quality, Stabilit America strives to contribute to more sustainable construction practices, helping shape a future where building materials improve quality of life while minimizing environmental impact. This dual focus on innovation and sustainability showcases Stabilit’s dedication to leading the industry toward a more responsible and forward-thinking approach to construction.
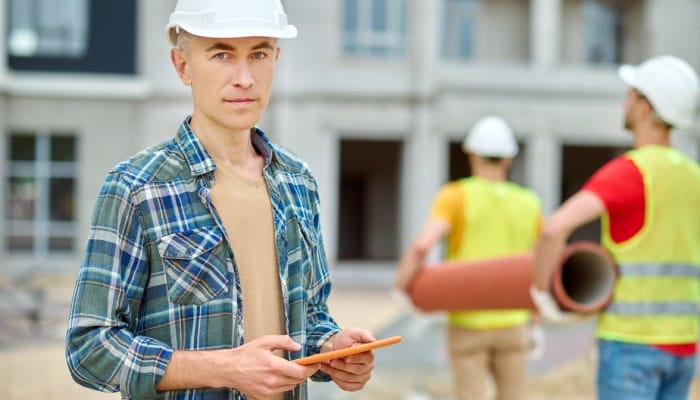
Discover the Stabilit Difference
From our inception, Stabilit America has been at the forefront of materials innovation, continually pushing the boundaries of what’s possible in architectural and industrial applications. As we look to the future, Stabilit America remains committed to pioneering new solutions that enhance both the aesthetic and functional demands of modern construction. Learn how Stabilit America’s cutting-edge materials can revolutionize your next project. Contact our team for more information and to explore our wide range of products designed for durability and performance.
Stabilit America Inc. is a leading North American manufacturer of fiberglass reinforced panels (FRP) and polycarbonate sheets, with over 65 years of experience. The company offers the widest range of acrylic, polyester, and polycarbonate laminates, backed by international certifications (USDA, Greenguard, FM, ISO 9001, among others), serving industries such as industrial construction, transportation, and sustainable building.
In the competitive market of travel trailer production, large bunkhouse models stand out for their spacious design and versatility. For manufacturers and rental companies, it is important to make sure that these trailers are functional, durable, and visually appealing. Stabilit America’s innovative fiberglass reinforced plastic (FRP) panels are the perfect solution. They blend durability with style, which is perfect for the demanding environments these trailers often encounter.
Understanding Large Bunkhouse Travel Trailers
Large bunkhouse travel trailers maximize sleeping capacity and living space, making them ideal for larger groups or families. These trailers typically feature multiple bunk beds and expansive living areas, catering to the needs of renters who require more room and comfort when they are traveling. Their popularity comes from their ability to provide a home away from home, with enough space to comfortably accommodate groups without feeling cramped.
Why FRP Panels Are Crucial for Bunkhouse Trailers
FRP panels, like those from Stabilit America, are particularly suited for large bunkhouse travel trailers used by rental companies. Here’s why these panels are essential:
Durability
Stabilit’s FRP panels, crafted with a special acrylic gelcoat, allow your large bunkhouse trailers to meet whatever demands come their way. The trailer external wall FRP panels provide protection against UV radiation and harsh weather conditions, which is something that these units have to stand up against throughout their extensive rental use. This lasting resilience means that your trailer’s exterior maintains its integrity and appearance, avoiding the typical wear and tear seen in less robust materials. For rental companies, this means extended service life and reduced frequency of replacements. It translates into cost savings and less operational downtime.
Aesthetic Appeal
The look of a travel trailer can be just as important as its functionality, especially in the competitive rental market. Stabilit’s Versalit Premium panels offer a high-gloss, mirror-like finish that elevates the visual appeal of large bunkhouse trailers. They are highly attractive to potential renters. This aesthetic enhancement helps you maintain a modern fleet, attracting a higher volume of customers looking for a premium rental experience. An attractive trailer exterior can often be the deciding factor when renters compare their options. When you use FRP panels for your large bunkhouse trailers, you get a distinct advantage in the rental market.
Maintenance
The amount of time large bunkhouse travel trailers spend on the road puts maintenance to the test as they cycle through all of the renters. What FRP panels can provide for maintenance is unmatched by any other materials. The ease of maintenance provided by FRP panels is unmatched, particularly valuable for trailers that cycle through numerous renters. The moisture and mildew resistance of the trailer wall FRP panels means they can be easily cleaned for the next customer without extensive labor. In turn, your trailers spend more time on the road and less time getting needed upkeep. This is really beneficial for large bunkhouse trailers that require quick turnaround times during busy rental periods. When you are running a rental business, these panels reduce the need for frequent deep cleanings and mitigate potential damage from constant use, keeping maintenance costs low and efficiency high.
Environmental Resistance
Large bunkhouse trailers equipped with FRP panels can face diverse climatic conditions without suffering deterioration. Whether your unit is up against the scorching sun, high humidity, or heavy rain, the superior weathering properties of these panels keep the structure from becoming compromised. This robust environmental resistance is important for trailers that are constantly moving across different regions, giving you the assurance that your investment is protected against the elements. This reliability not only preserves your trailer’s lifespan but also enhances its usability across all kinds of environmental conditions.
The Benefits of Versalit and Steeliner FRP Panels
Stabilit America offers two distinct lines of FRP panels—Versalit and Steeliner—each with unique benefits suited to the demanding environments of large bunkhouse travel trailers:
- Versalit Panels: Versalit panels, offered in premium, low-gloss, and pebble flex finishes, are engineered to combine flexibility with extraordinary strength. The Versalit Premium’s high-gloss, mirror-like finish makes your trailer look great while holding up against extreme weather conditions. That means your trailer’s exterior remains pristine over time. This durability is backed by UV stabilization, which protects the panels from sun damage and contributes to their long lifespan. As a result, your panels require less frequent replacements and can maintain a higher resale value.
- Steeliner Panels: Steeliner panels are designed to meet the rugged demands of travel trailer exteriors like the walls and roofs. These panels withstand high impacts and abrasions, giving the best protection against road debris and environmental wear that comes with long travel miles. Their built-in moisture resistance prevents rust and mildew, enhancing the health of the interior parts of your trailer and reducing the maintenance burden. Additionally, Steeliner’s ability to resist chemical exposures ensures that the trailer’s appearance and function are not compromised, supporting a longer service life and greater customer satisfaction.
Interior Applications of FRP Panels in Large Bunkhouse Trailers
Additionally, the interior durability and aesthetic appeal significantly impact the value and desirability of large bunkhouse trailers. Manufacturers and rental companies, therefore, are increasingly turning to innovative solutions like FRP panels for all of their interior walls and ceilings in every unit.. Let’s explore specific interior applications where these panels can truly shine.
- Wall Linings: FRP panels are perfect for lining the walls of bunkhouse trailers, offering a sturdy surface that resists dents and scratches from luggage or furniture movement. Their smooth finish makes them easy to clean. That helps you keep a fresh environment after each rental period.
- Bathroom Surfaces: You can utilize the water-resistant properties of FRP panels in the bathroom areas. They prevent moisture penetration and mold buildup, ensuring the bathrooms remain dry and hygienic, prioritizing your guests’ health and comfort.
- Kitchen Backsplashes: Incorporate FRP panels as kitchen backsplashes to protect against splashes and stains. Their chemical resistance means cleaning up is a breeze, no matter how adventurous the cooking gets.
- Ceiling Panels: When you use FRP panels on the ceilings they provide a consistent, clean look that helps with moisture management, especially in humid conditions. This helps maintain the structural integrity of your trailer’s space, stopping water damage and sagging from occurring.
- Decorative Touches: You can get FRP panels in different textures and colors to create interior designs that differentiate your trailer from all of the competition that is out there.
Why This Matters to Manufacturers and Rental Companies
For manufacturers, using Stabilit America’s trailer wall FRP panels means producing travel trailers that stand out for their quality and durability, increasing appeal to potential buyers and renters. Rental companies benefit from enhanced durability and low maintenance, ensuring a longer lifespan and reduced operational costs for their fleet. Additionally, the aesthetic flexibility of these panels allows for customized designs that can cater to various customer preferences, adding a competitive edge in the market.
Elevate Your Fleet With Stabilit America’s FRP Panels
Embrace the future of large bunkhouse travel trailers with Stabilit America’s FRP panels. Whether you’re manufacturing these trailers or managing a rental fleet, our panels offer the durability, aesthetic appeal, and low maintenance you need to stay ahead in the market. Invest in Stabilit America’s FRP solutions and deliver a superior travel experience that customers will choose time and again. Discover how our FRP panels can transform your trailer offerings. Contact us today to learn more and start differentiating your products in the bustling travel trailer market.
Stabilit America Inc. is a leading North American manufacturer of fiberglass reinforced panels (FRP) and polycarbonate sheets, with over 65 years of experience. The company offers the widest range of acrylic, polyester, and polycarbonate laminates, backed by international certifications (USDA, Greenguard, FM, ISO 9001, among others), serving industries such as industrial construction, transportation, and sustainable building.
Cutting FRP (Fiber-Reinforced Plastic) panels requires precision and care to ensure a clean, safe, and effective result. This tutorial will guide you through the necessary steps, tools, and techniques to cut FRP panels effectively and safely.
Tools and Materials Needed
Before you start cutting your FRP panels, make sure you gather the right tools and prepare your workspace. This preparation helps ensure the quality of your cuts and keeps you safe as you work. Here’s a rundown of what you’ll need to achieve clean and precise cuts:
- Safety Gear: Use some safety goggles, gloves, and a dust mask to protect yourself from any small particles and sharp edges.
- Circular Saw: Equip a circular saw with a carbide-tipped blade for straight cuts and a smoother finish.
- Jigsaw: For curves and detailed shapes, use a jigsaw with a fine-toothed blade.
- Tape Measure and Marker: Accurately measure and clearly mark where you’ll cut.
- Straight Edge or Ruler: Use this to guide your cuts and ensure they remain straight.
- Clamps: Secure the panel to your work surface to prevent movement during cutting.
- Dust Extraction System or Vacuum: Manage FRP dust, which can be hazardous, by using a dust extraction system or vacuum.
Preparation
Next, you need to work on setting up your workspace. This step is just as important as the cut itself. You need a space that not only allows for accurate work but also keeps you safe from the fine particulates that arise during the cutting process. Here’s how you can optimize your workspace and ensure your measurements and setup are precise for the task at hand.
- Workspace Setup: Make sure the area you are going to be working in is well-ventilated to manage dust. Setting up outdoors would be your best option, but if you need to work indoors, check for good airflow.
- Measuring and Marking: Use the tape measure to determine where you need to cut. Mark the cutting line with a marker so you can see it when you are ready to make your cut. A straight edge can help in drawing precise lines.
- Securing the Panel: Use clamps to secure the FRP panel to your work surface. This prevents the panel from moving and reduces the risk of chipping.
Cutting Techniques
Cutting FRP panels accurately is how you make sure your construction or renovation projects are successful. Whether you’re using a circular saw or a jigsaw, the right techniques can make all the difference. Here is how you can successfully utilize these tools to get precise cuts without compromising on safety or quality.
Using a Circular Saw:
When you cut FRP panels with a circular saw, make sure you use a carbide-tipped blade. This type of blade is specifically designed for cutting composite materials like FRP. That means it provides a cleaner cut with less risk of chipping. Before you start, adjust the blade depth to just slightly more than the thickness of the panel. This setting helps minimize chipping and allows the blade to cut through the panel efficiently. Place the panel securely on your work surface and align the saw blade with the marks you made during the preparation phase. Guide the saw along a straight edge so the cut is perfectly straight. Forcing the saw can give you uneven cuts and potentially damage the panel or your tool, so make sure you move the saw steadily.
Using a Jigsaw:
Another option for more intricate cuts or when you need to make internal cutouts is a jigsaw. Start by attaching a fine-toothed blade to your jigsaw, which is ideal for cutting synthetic materials or metals. It gives you smooth edges and precise cuts. If your cutout starts from the interior of the panel, drill a hole large enough to accommodate the jigsaw blade at one end of your intended cut. This hole serves as the starting point for your jigsaw. Carefully insert the blade into this hole and align it with your marked line. As you cut, guide the jigsaw along the line smoothly, maintaining a steady pace to avoid jagged edges or deviations from your intended path. The jigsaw is perfect for creating detailed shapes and curves that a circular saw might not handle the same way.
CNC Cutting
For high-precision and complex pattern needs, CNC cutting is the best solution. Start programming your design into the CNC machine. Choose a diamond-coated cutting tool appropriate for the abrasiveness of FRP panels. Once the panel is securely mounted on the CNC bed, the machine precisely follows the programmed path, providing exact cuts with smooth edges and minimal need for post-processing.
Using Routers
Routers are great for trimming and shaping the edges of your FRP panels, whether creating bevels, rounded edges, or detailed profiles. Select a router bit that can withstand the hardness and abrasiveness of FRP, such as ones made from tungsten carbide or diamond-tipped materials. Secure the panel and carefully adjust the router’s depth during multiple passes to refine edges and achieve detailed contours without chipping. This method is perfect for detailed edge finishing and complex profiling.
Handheld Shears
When you need quick and versatile cuts without setting up heavy machinery, handheld shears are the perfect option. They come in electric, pneumatic, and manual types:
- Electric and Pneumatic Shears: These shears are powered and provide effortless cutting action. They work well when you are cutting large volumes of FRP panels or thick materials.
- Manual Shears: Manual shears work best for small projects or on-site adjustments where power tools are impractical. Manual shears require more physical effort but offer maximum control and the ability to make quick, small cuts without the setup of powered tools.
Safety Tips
From wearing the right protective gear to managing dust, you need to take steps to prevent injury. Here’s how to keep your cutting process safe and efficient, protecting both you and your workspace from potential hazards:
- Wear Protective Gear: Always wear your safety goggles, gloves, and a dust mask when cutting FRP panels.
- Dust Management: Use a dust extraction system or a shop vacuum attached to your saw to minimize airborne particles.
- Check for Obstructions: Before cutting, ensure there are no obstructions like nails or metal fasteners along the cutting line.
- Blade Sharpness: Regularly check the sharpness of your blades. Dull blades can cause chipping and require more force, which is unsafe.
Post-Cutting Cleanup
After successfully cutting your FRP panels, properly handling the remnants and smoothening the edges ensures your finished project looks polished and professional.
- Cleaning Edges: After you finish cutting, the edges of the FRP panels might be slightly rough or sharp. Use fine-grit sandpaper to smooth out the edges.
- Dust Cleanup: Clean up all dust and debris from cutting immediately, especially if working indoors. Dispose of the dust safely according to local regulations.
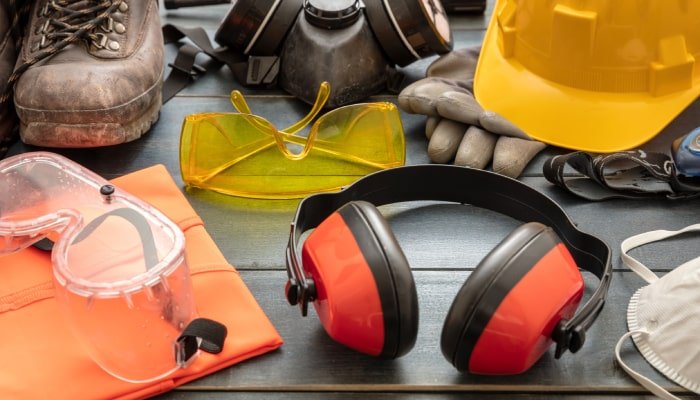
Enhance Your Cutting Skills with FRP Panels Today
If you’re ready to elevate your construction projects with precision cutting techniques and the best FRP materials, explore our range of high-quality FRP products by application. At Stabilit America, a leading FRP panels manufacturer, we are committed to providing you with the best materials and guidance so your projects exceed expectations. Start achieving cleaner, more efficient cuts today and see the difference in your next construction or renovation project.
Stabilit America Inc. is a leading North American manufacturer of fiberglass reinforced panels (FRP) and polycarbonate sheets, with over 65 years of experience. The company offers the widest range of acrylic, polyester, and polycarbonate laminates, backed by international certifications (USDA, Greenguard, FM, ISO 9001, among others), serving industries such as industrial construction, transportation, and sustainable building.
When it comes to construction and design, material choice matters. At Stabilit America, our twin wall polycarbonate panels stand out for their exceptional performance and versatility. Twin wall polycarbonate panels have unique characteristics that make them perfect for your construction project.
Unique Characteristics of Twin Wall Polycarbonate Panels
In modern construction, material performance and versatility are key. Twin wall polycarbonate panels have some great advantages that make them an excellent choice for your construction project as you leverage them to make the most of the space you are creating.
Lightweight and Durable
Twin wall polycarbonate panels are significantly lighter than traditional glazing materials like glass, which simplifies handling and installation. For instance, a 4mm thick panel weighs only 0.16 lb/ft (800 g/m), making it easy to maneuver without compromising strength. Despite how lightweight they come, these panels are highly impact-resistant, being capable of withstanding extreme weather conditions and physical impacts. That means you can offer long-lasting performance and reduced maintenance costs to your clients.
Superior Light Transmission
Another feature of twin wall polycarbonate panels is their excellent light transmission. Depending on the thickness, these panels allow 80% to 82% of light to pass through, ensuring great natural lighting for any space. This is particularly beneficial in applications such as greenhouses and sports halls, where natural light is needed for both plant growth and energy savings. By maximizing natural light, you can create brighter, more inviting spaces while reducing reliance on artificial lighting.
Long-Lasting UV Protection
Engineered to resist prolonged exposure to sunlight, our twin wall polycarbonate panels feature a co-extruded UV-protected PC layer fused to the substrate. That means your panels won’t turn yellow or lose light transmission over time. This durability is backed by a 10-year non-prorated warranty, offering peace of mind and long-term cost savings. The UV protection maintains the panels’ clarity and performance, making them a reliable choice for outdoor applications where exposure to the elements is inevitable.
Thermal and Acoustic Insulation
Twin wall polycarbonate panels also provide superior insulation properties. These panels enhance energy efficiency and improve the overall comfort indoors.
Thermal Insulation
The air gap between the two layers of polycarbonate helps maintain stable indoor temperatures by reducing heat transfer. This insulation property significantly cuts down on the need for artificial heating and cooling, leading to energy savings. For instance, a 10mm thick panel offers enhanced thermal insulation compared to thinner panels, making it a great option for structures that need stringent temperature control.
Acoustic Insulation
These panels provide effective acoustic insulation. The dual-layer structure helps reduce noise transmission, creating a quieter area. For example, a 6mm thick panel has a sound reduction index of 10, while a 10mm panel offers an index of 16, making them perfect for settings where noise control is essential, such as sports halls and residential buildings.
Best Uses in Construction and Design
With all of the impressive features, twin wall polycarbonate panels offer versatile solutions tailored to all types of construction and design projects. In the construction industry, understanding the best applications of these panels can enhance project efficiency and client satisfaction.
Industrial and Commercial Applications
Twin wall polycarbonate panels work well for industrial and commercial buildings where you need heat-insulating glazing. These panels provide natural light while maintaining thermal efficiency, making them the perfect choice for factories, warehouses, and other large facilities. By incorporating these panels, you can reduce the need for artificial lighting and maintain consistent indoor temperatures, resulting in lower operational costs and improved energy efficiency.
Architectural Designs
Architects appreciate these panels for their flexibility and aesthetic appeal. They are widely used in public buildings, hotels, and sports facilities, offering both form and function. Their lightweight nature and ease of installation allow for creative design possibilities without compromising structural integrity. This versatility makes them perfect for innovative architectural projects where visual appeal and practical performance are equally important.
Residential Projects
For residential construction, twin wall polycarbonate panels are an excellent choice for light roofing in patios, verandas, and greenhouses. Their superior light transmission and thermal insulation properties enhance living spaces by providing natural light and maintaining comfortable temperatures. The ease of installation makes it good for DIY enthusiasts and professional contractors. They are a practical option for various residential applications. By using these panels, you can offer homeowners bright, energy-efficient spaces with reduced heating and cooling costs.
Structural Considerations
When incorporating twin wall polycarbonate panels into your projects, it is essential to consider structural factors such as load deflection and heat expansion.
Load Deflection
Before you start construction, make sure your structure can handle the forces applied by wind and snow loads. The total applicable load should not cause deflection beyond 5% of the dimensions of the shorter side of the sheet. This precaution ensures both safety and aesthetic integrity.
Heat Expansion
Polycarbonate has a higher heat expansion coefficient than materials like glass, steel, and aluminum. Make sure you calculate specific clearance between the sheet and the structural frame to account for thermal expansion and prevent issues during installation.
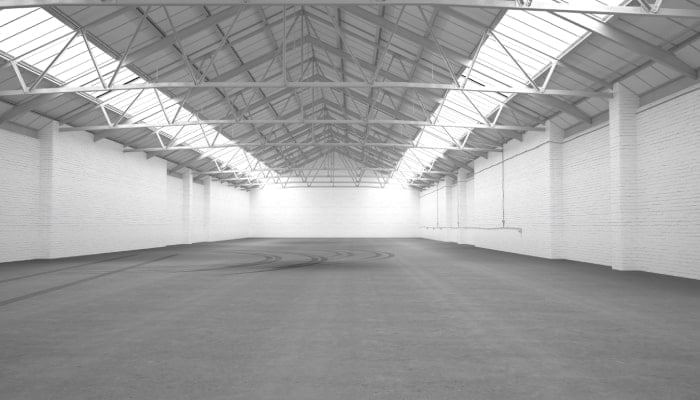
Enhance Your Projects with Twin Wall Polycarbonate Panels Today
Twin wall polycarbonate panels offer a blend of durability, light transmission, and energy efficiency, so you can use them in a wide range of construction and design applications. At Stabilit America, we are dedicated to providing high-quality solutions that meet the needs of professionals in the field. For more information on our multiwall polycarbonate panels, visit our website. Explore our range of multiwall polycarbonate panels and learn more about how we can support your construction needs. As a leading FRP panels manufacturer, we are committed to excellence in every panel we produce.
Stabilit America Inc. is a leading North American manufacturer of fiberglass reinforced panels (FRP) and polycarbonate sheets, with over 65 years of experience. The company offers the widest range of acrylic, polyester, and polycarbonate laminates, backed by international certifications (USDA, Greenguard, FM, ISO 9001, among others), serving industries such as industrial construction, transportation, and sustainable building.